MBR Building
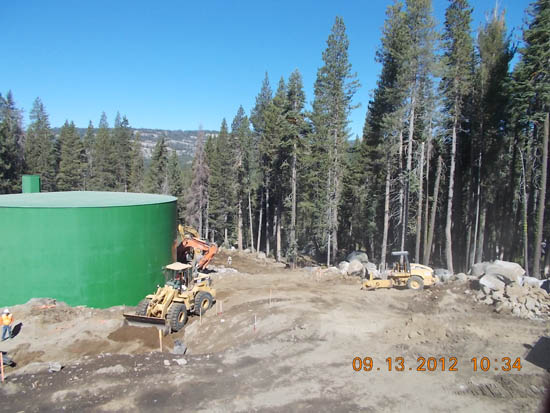
Underground piping at the MBR Building
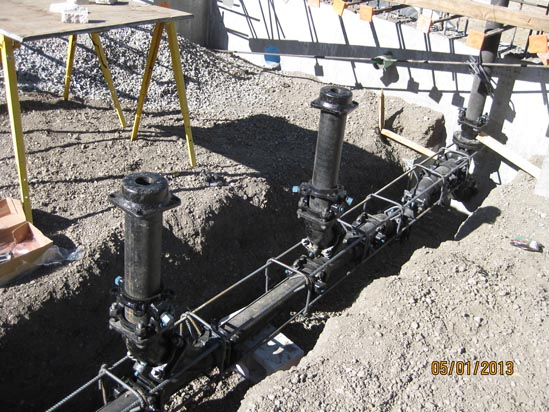
Underground piping at the MBR Building
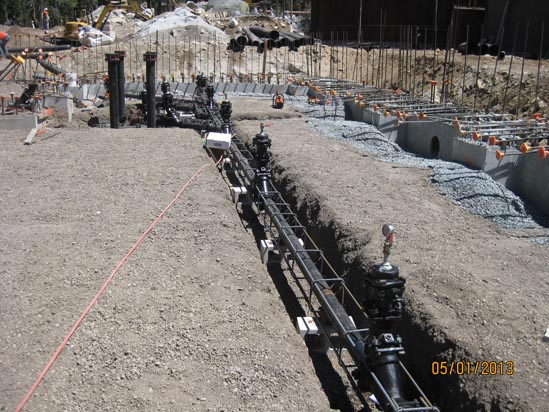
Underground piping at the MBR Building
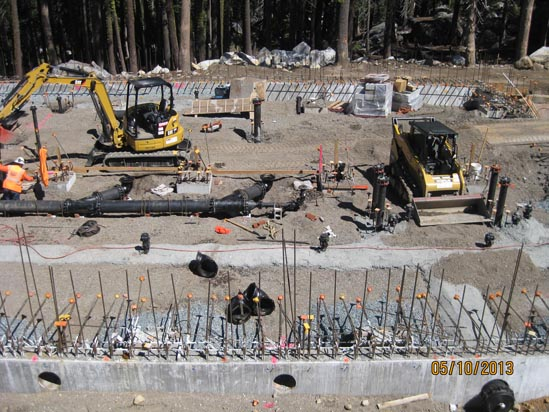
Trenching for underground pipe at the MBR Building
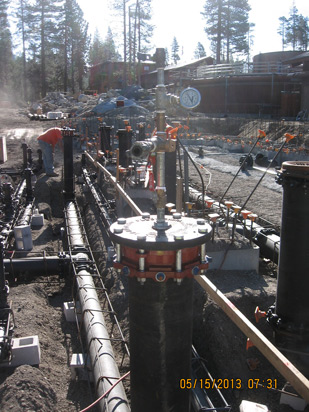
Underground piping at the MBR Building
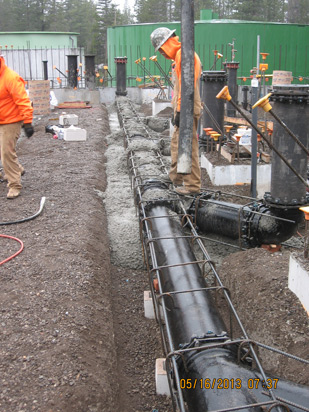
Underground piping at the MBR Building
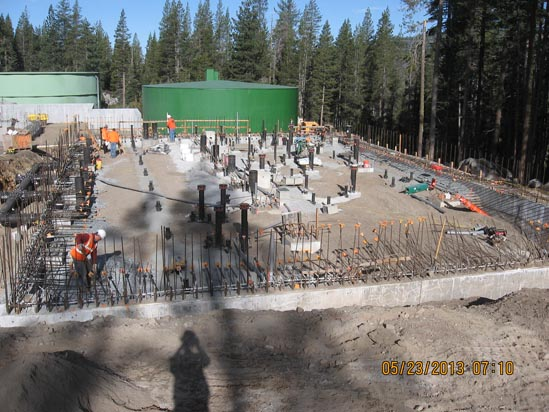
Backfill completed at the MBR Building
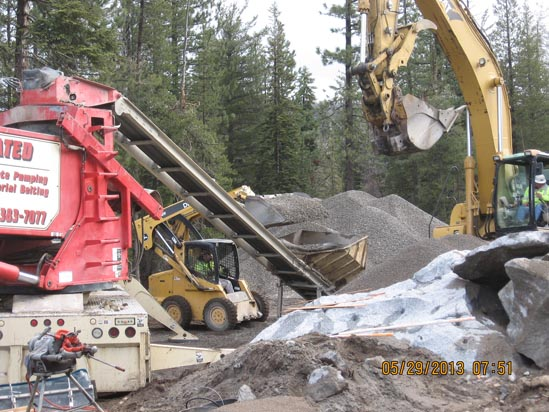
Backfill equipment for the Membrane Building: Conveyor belt stretched out and feeds gravel and roadbase mix to pour into the void over the piping.
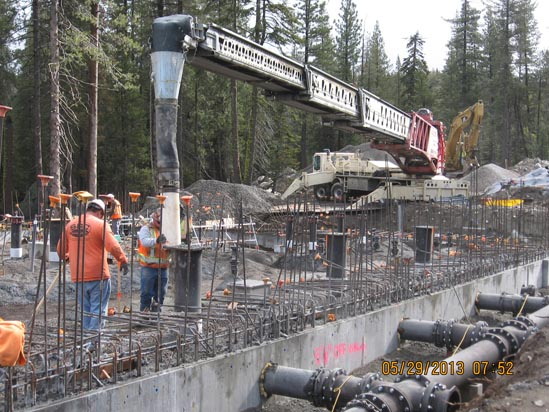
Backfill equipment for the Membrane Building: Conveyor belt stretched out and feeds gravel and roadbase mix to pour into the void over the piping.
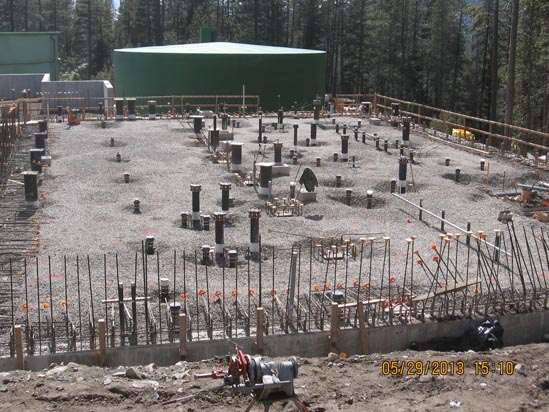
Backfill completed at the MBR Building
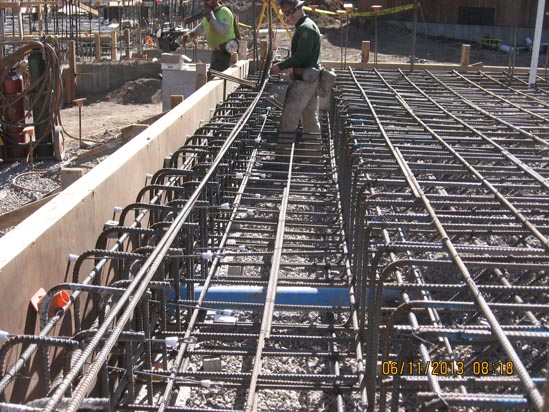
Tying rebar at the MBR Building
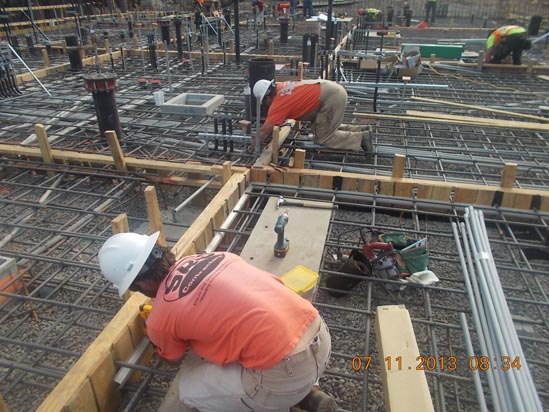
Putting up forms at the Membrane Building
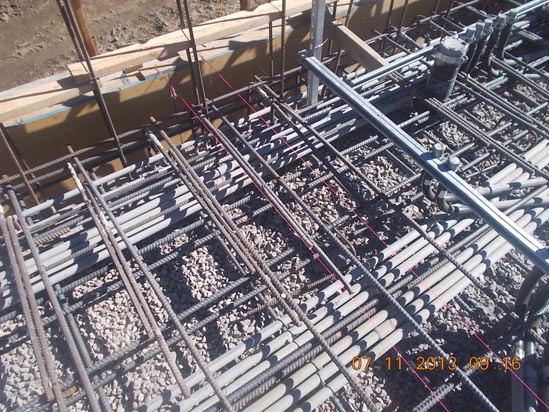
There are crazy amount of conduits on this project!
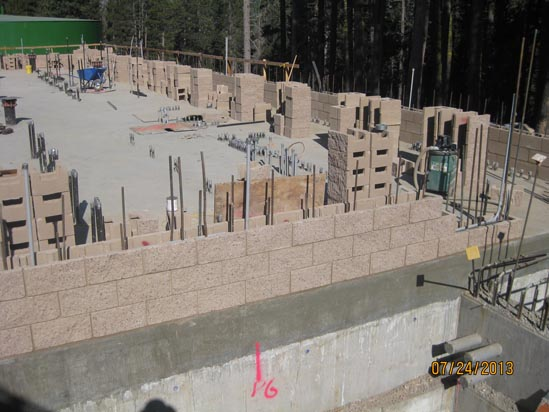
Laying brick at the Membrane Building
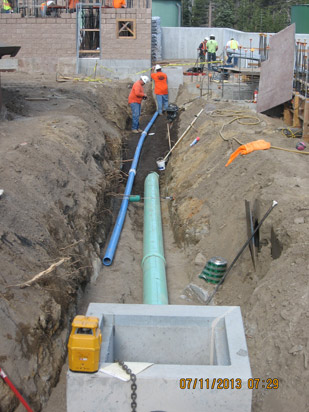
Four inch drain line for recycled water and 12 inch storm drain
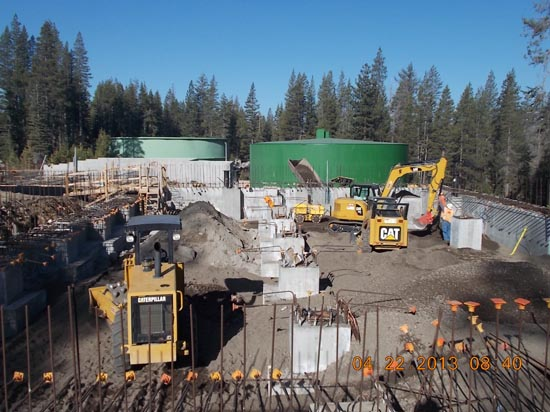
Backfilling: Adding dirt to raise the ground level over to cover the concrete pilings. The concrete flooring slab will be poured at the top of the walls.
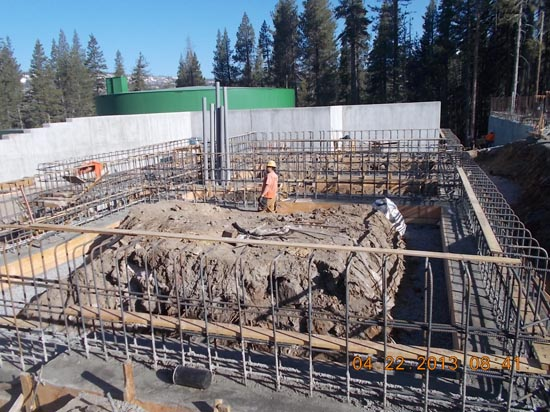
New membrane forms for MBR building
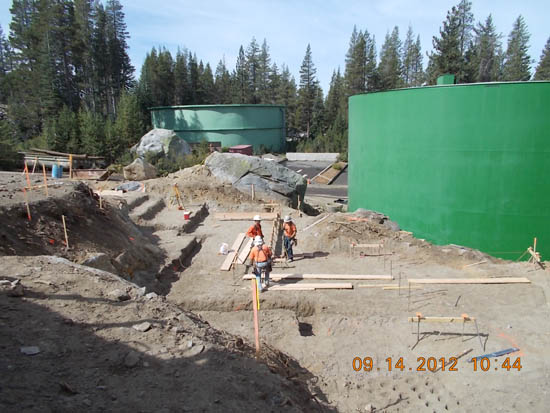
Looking northeast at the MBR building
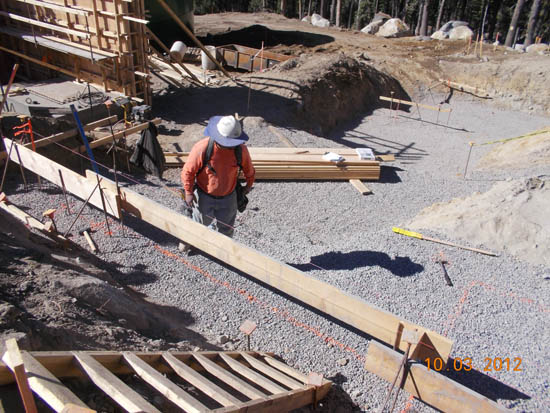
Labor hard at work on Donner Summit
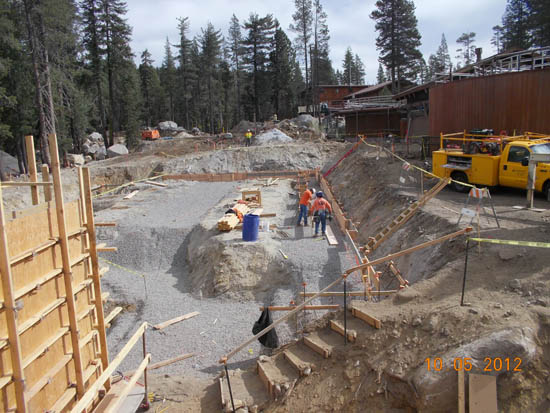
Looking east at new membrane building foundation and contractor temporary access stairs.
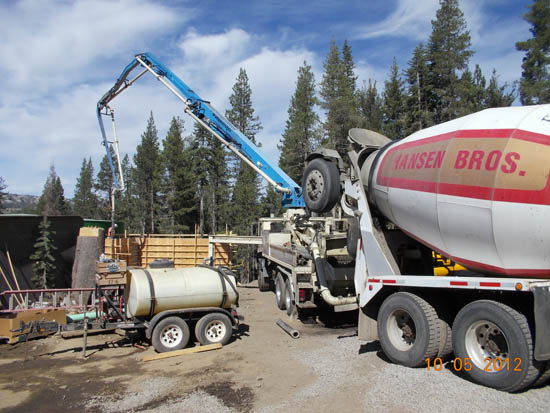
Pouring of the retaining wall for the MBR building west of the Chemical/Electrical building
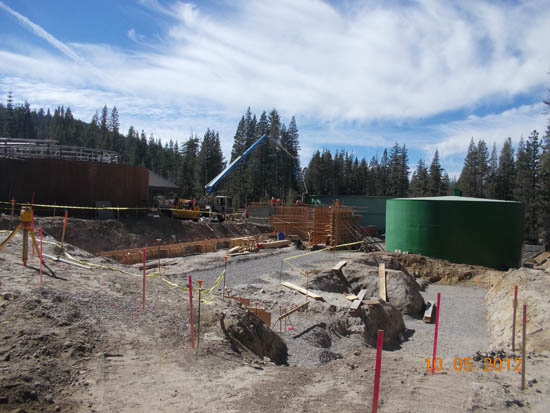
Pouring concrete for the MBR building showing the existing sludge tank
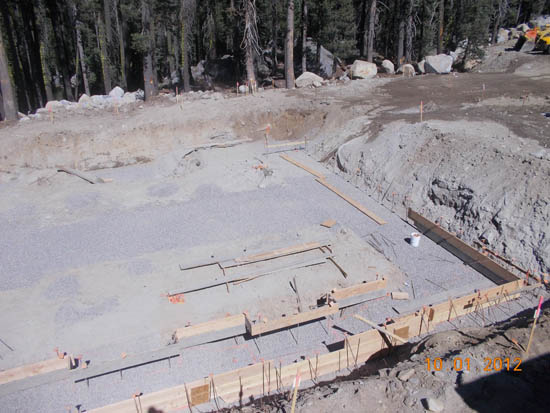
Laying out footing for the MBR building
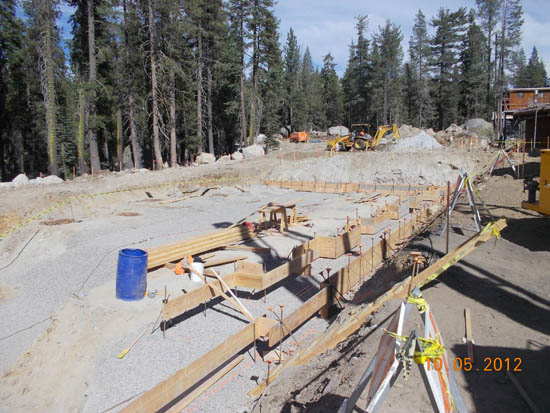
Northeast view of the MBR building
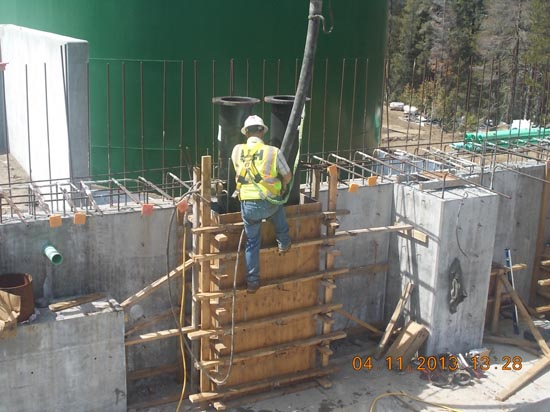
Pouring concrete into the form at the MBR building
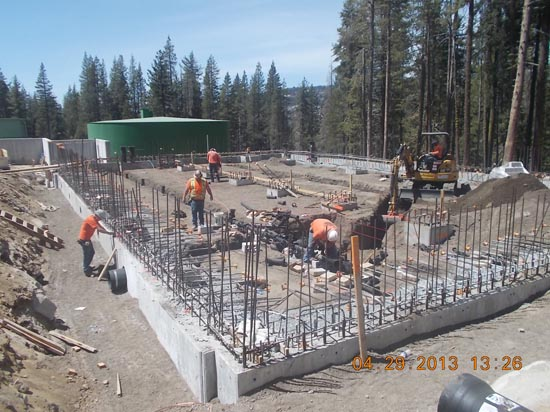
Underground piping being placed
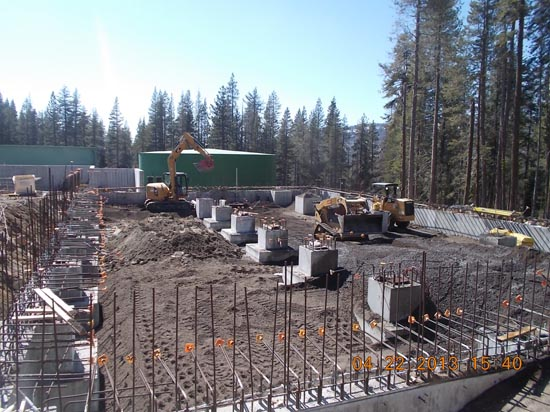
Backfilling: Added dirt to raise the ground level over to cover the concrete pilings. The concrete flooring slab will be poured at the top of the walls.
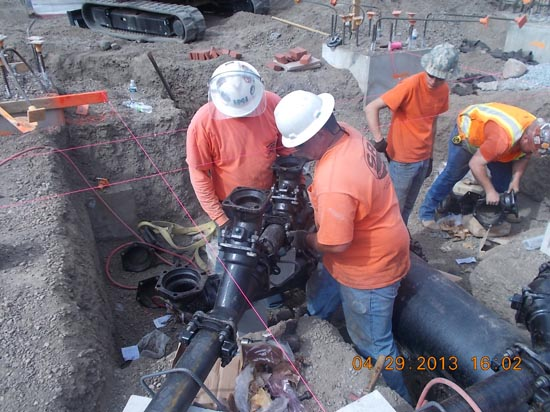
Fitting underground pipe
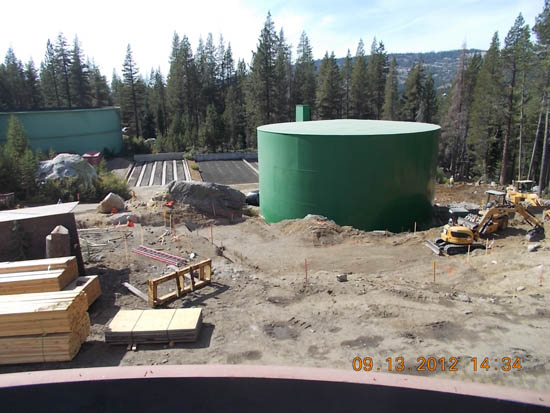
Site preparation for building which will house the MBR (membrane bioreactors)
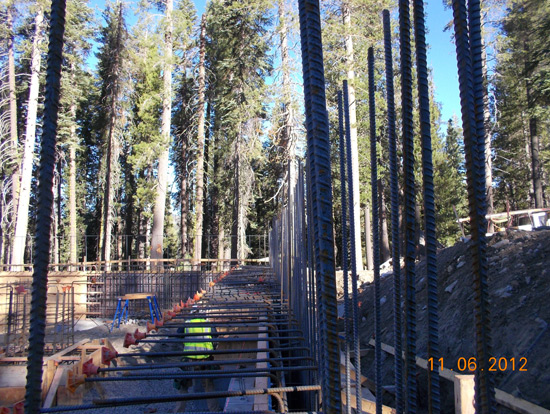
Workers yying iron for the MBR building.
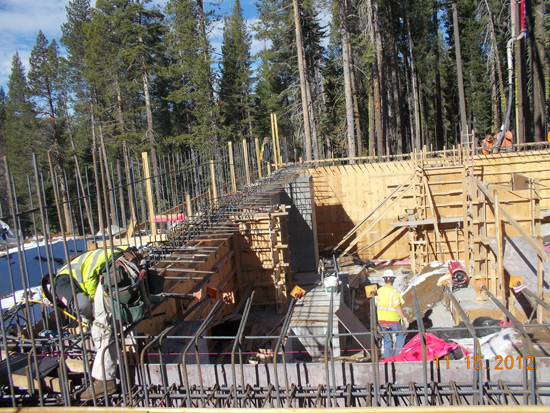
Concrete work at the MBR Building
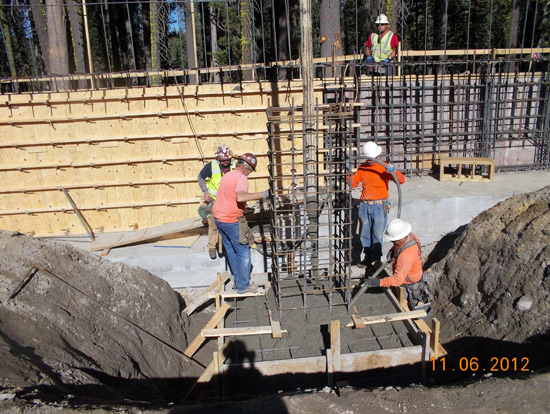
Workers tying steel at the MBR building. Note the footing pedestals. The pedestals that are formed into the outer walls are like pilasters because of their construction, but pilasters typically would travel to the top of the wall and support the roof or wall. *Complete text below
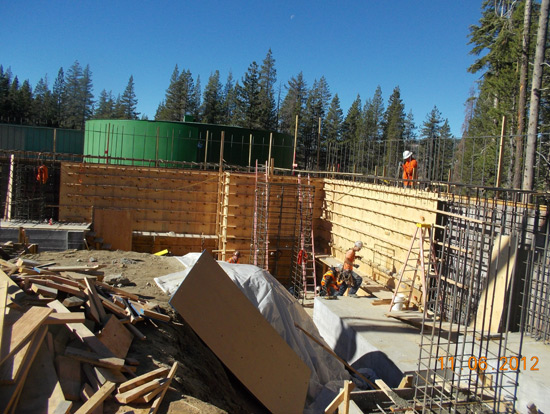
Forms for concrete retaining walls and footings for MBR building.
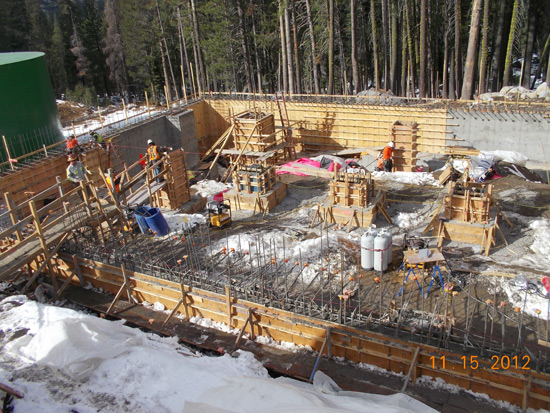
Concrete work at the MBR Building
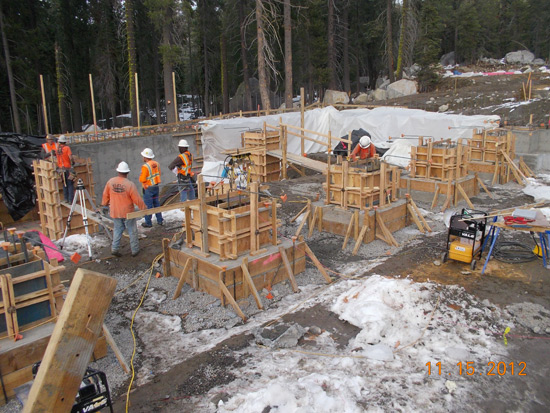
Concrete work at the MBR Building
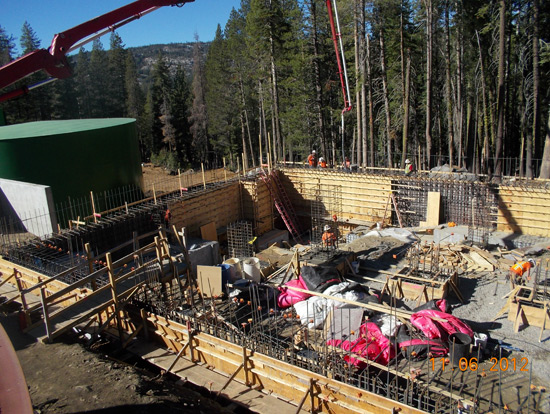
Forming up footings for MBR building
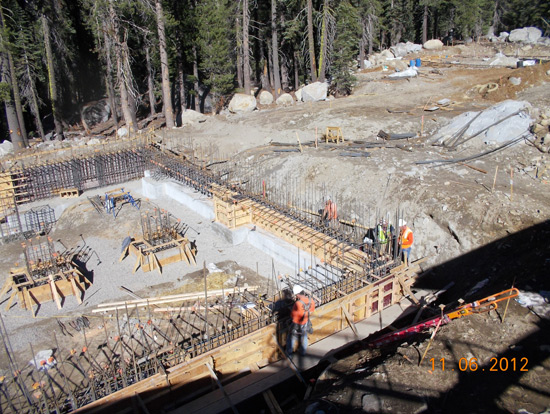
Forming up footings for MBR building.
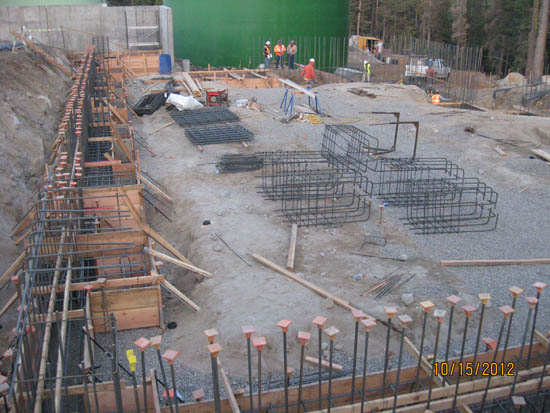
Laying out rebar, tying iron and forming for concrete pours of the footing of the MBR building
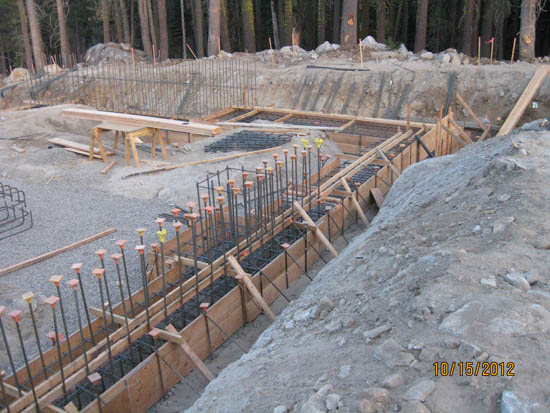
Laying out rebar, tying iron and forming for concrete pours of the footing of the MBR building
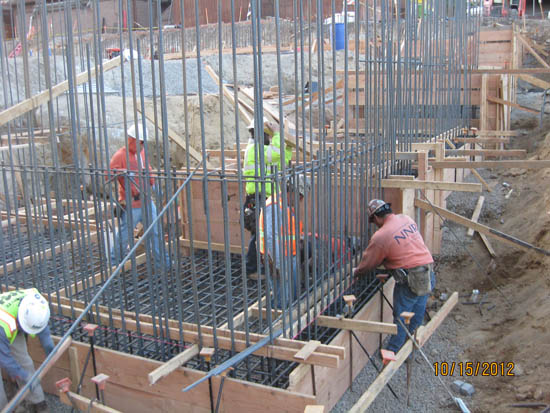
Tying iron for the footing for the new MBR building
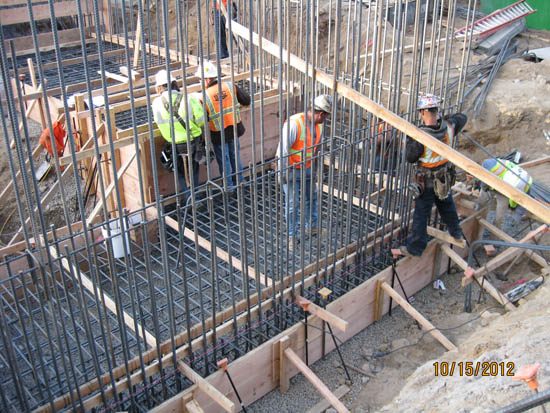
Tying iron for the footing for the new MBR building
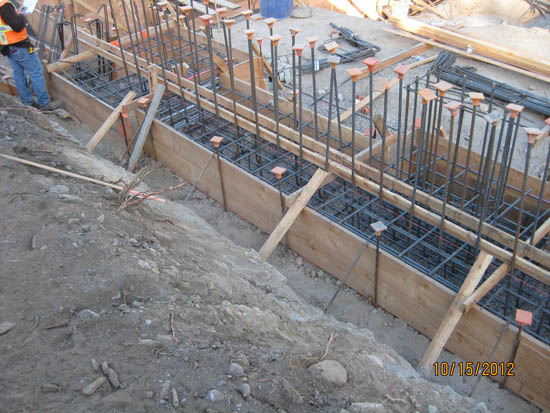
Forming and rebar placement for MBR building
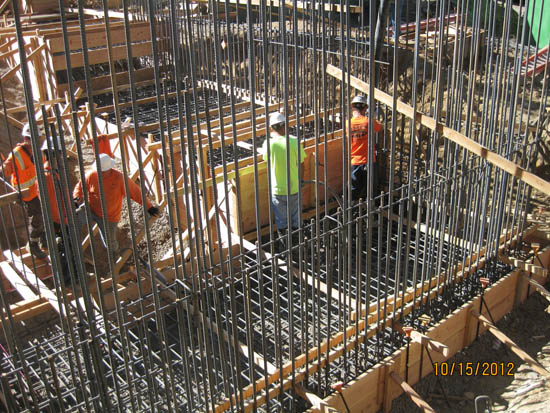
Tying iron for the footing for the new MBR building
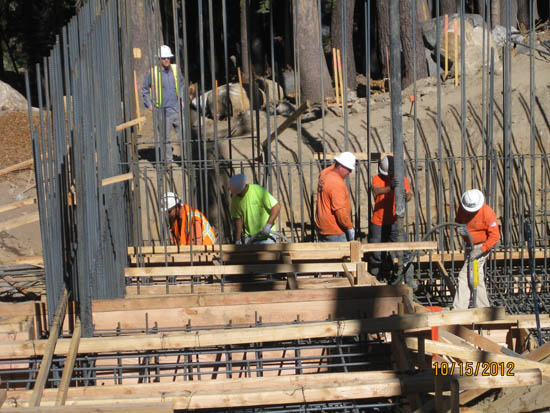
Pouring concrete for the footing of the MBR Building
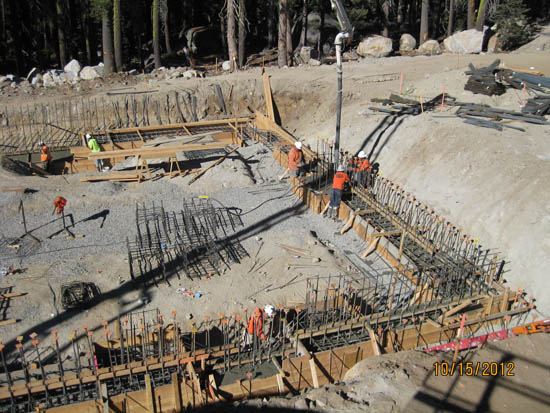
Pouring concrete for footing of the MBR building
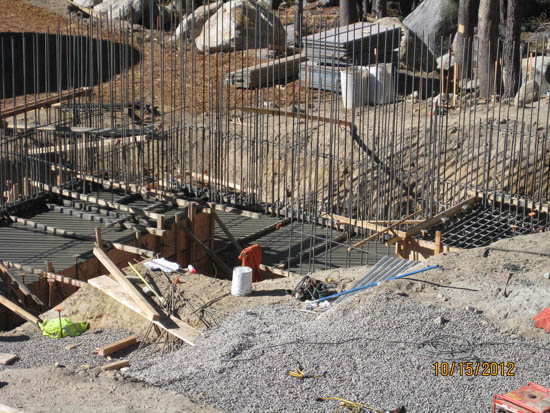
Concrete poured at the MBR building northwest corner of footing.
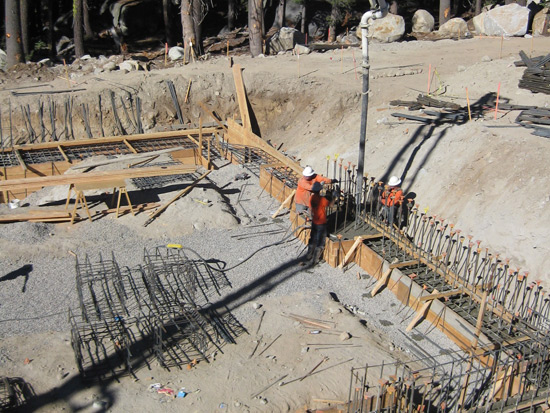
Pouring concrete for footing of the MBR building
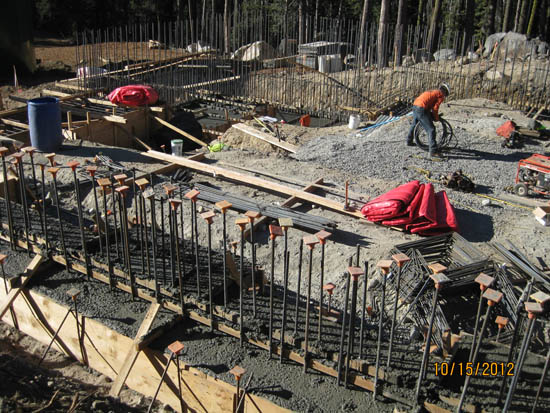
Pouring concrete for footing of the MBR building
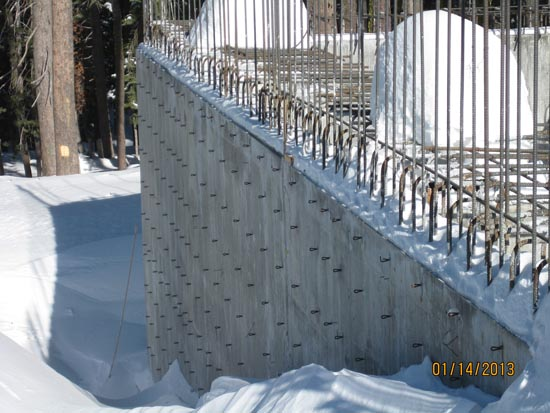
The corner of MBR building
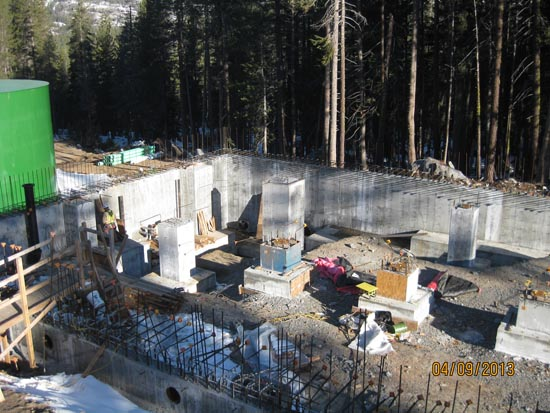
MBR building prior to backfill
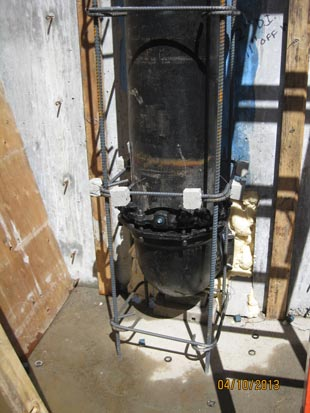
Southwest side of the MBR building
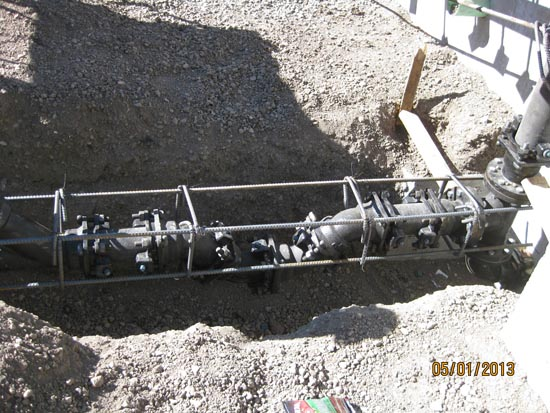
Underground piping to be encased concrete

Underground piping to be encased in concrete
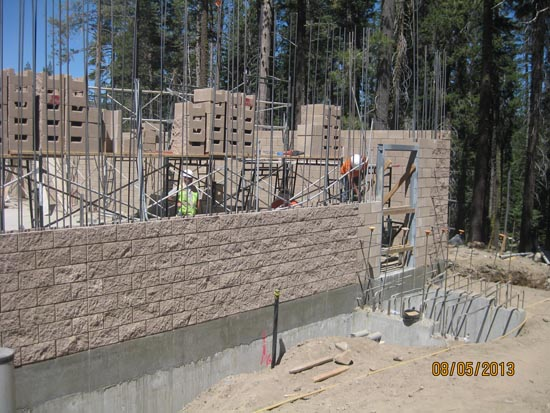
Construction brick walls at MBR building
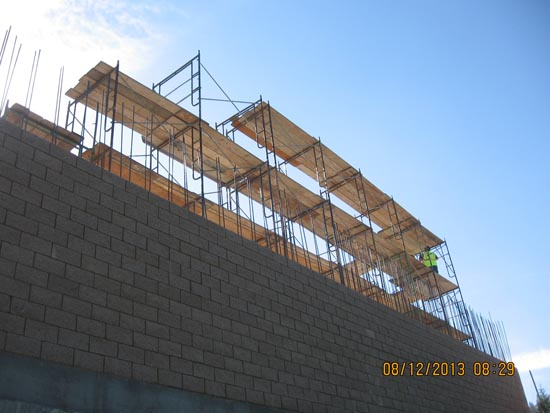
Scaffolding for brick layers at Membrane Building
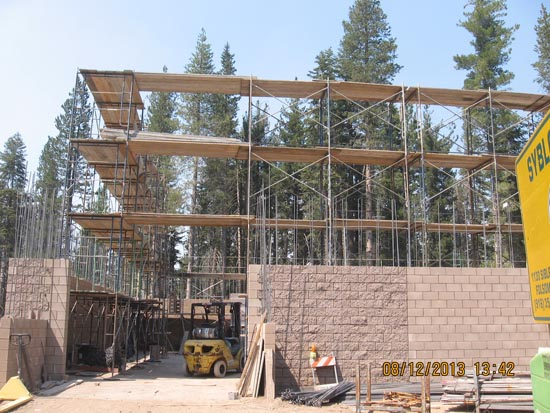
Constructing brick walls at MBR building
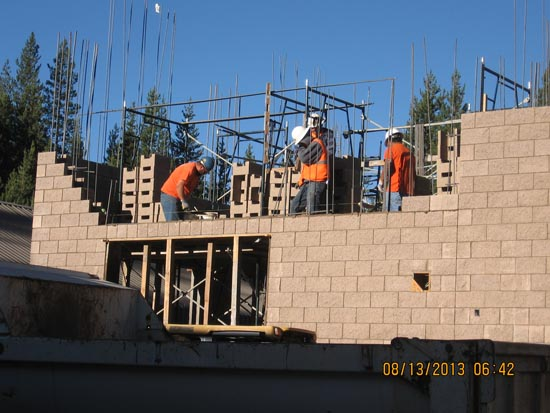
Constructing brick walls at MBR building
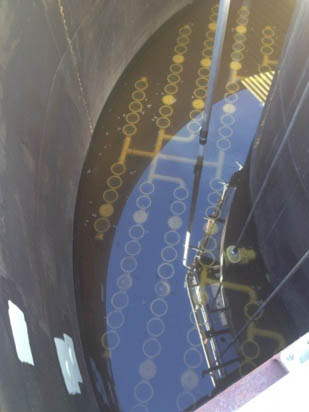
Aeration system in the Reactor #2 Tank
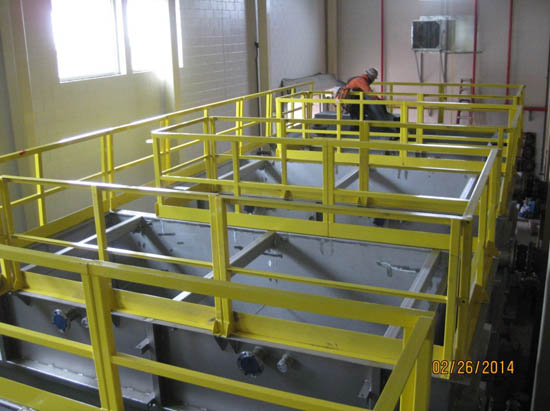
Membrane tanks with handrail and solid plank deck
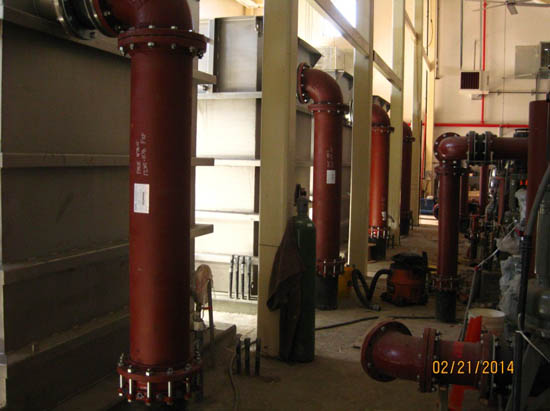
Membrane tank overflow piping installation
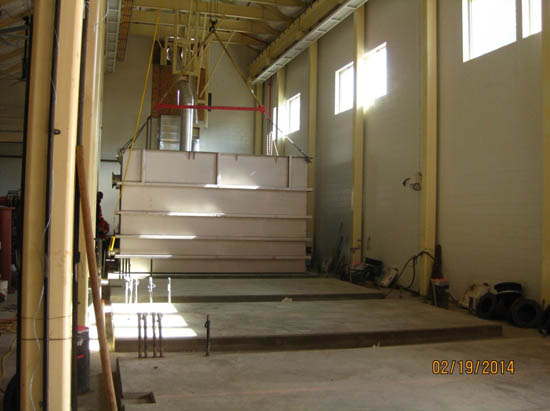
Using overheard crane to lift basin shells onto pads
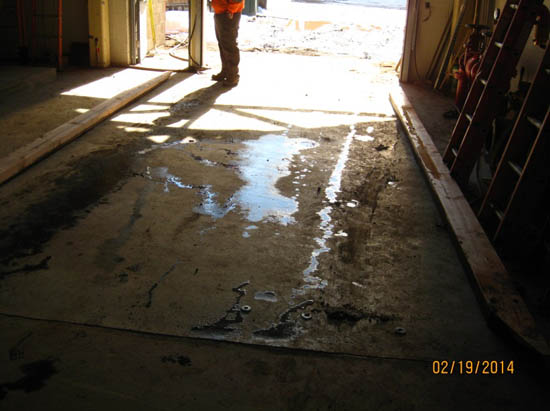
Skids removed from bottom of tanks before setting
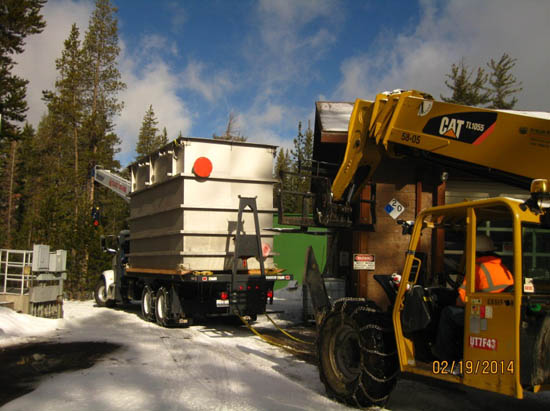
Moving first Membrane basin tank down to building
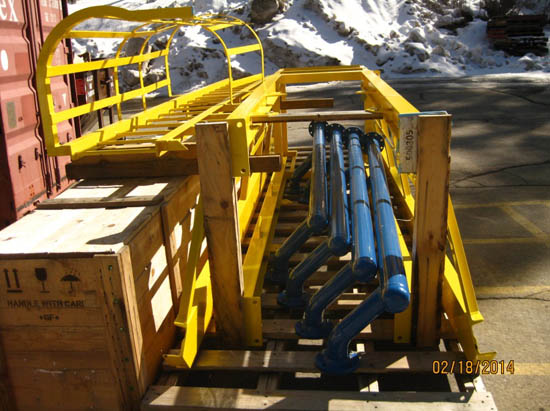
Ladders, handrails and misc. piping for Membrane tanks
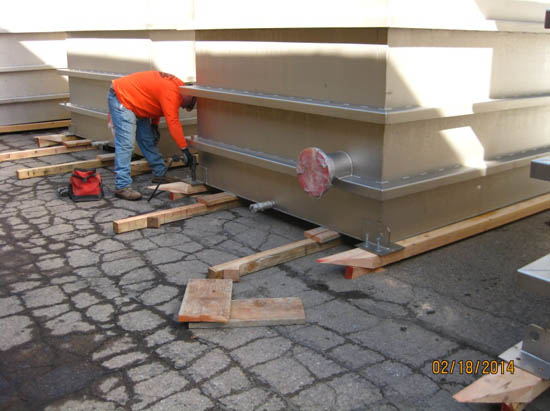
Installing wooden skids to move Membrane tank shells
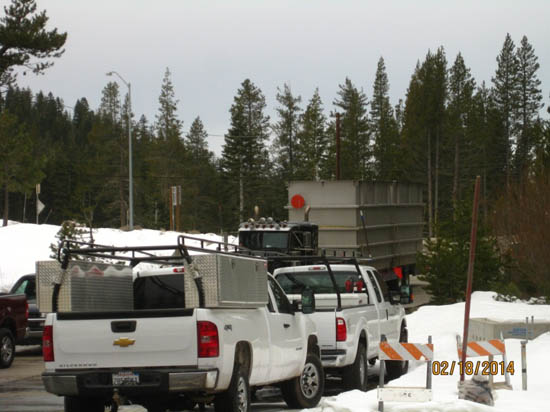
Membrane tank deliver from Folsom storage
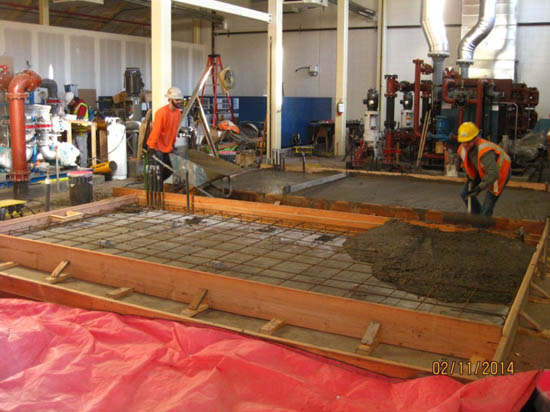
SR crew pours the four Membrane basin concrete slabs.

Pulling wire for power to Membrane Building at vault
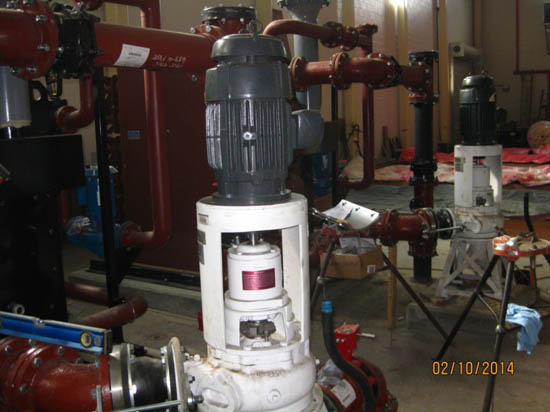
Heat exchanger recirculation pumps at Membrane Building
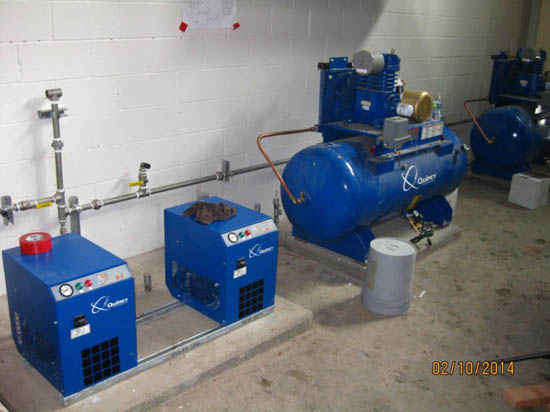
Instrument air system at east wall in the Membrane Building
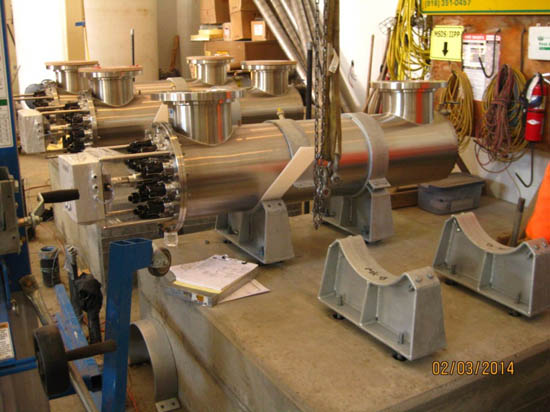
Installing UV treatment tubes at Membrane Building
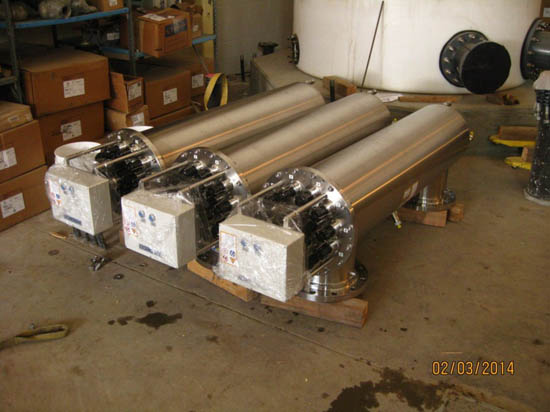
Delivery of UV treatment tubes to Membrane Building
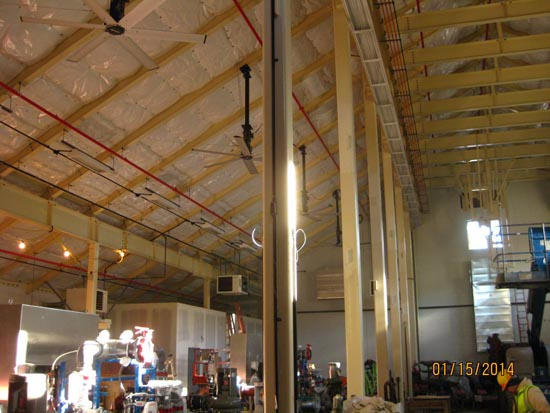
Destratification fans installed in Membrane Building
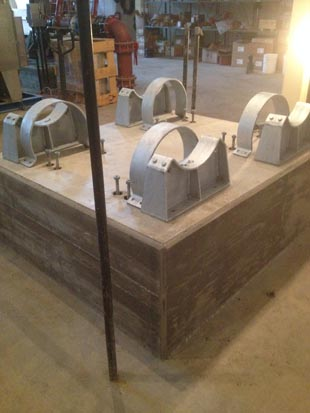
Preparing to set UV reactors
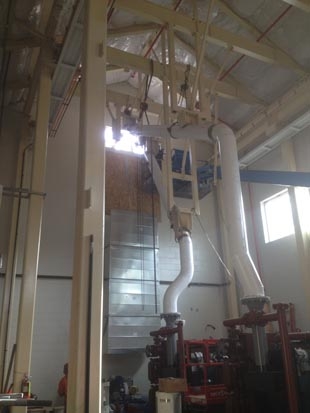
Heat exchanger exhaust line installation in Membrane Building
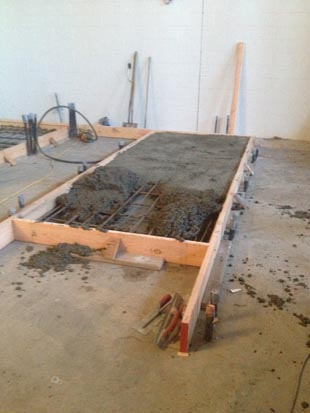
Membrane blower concrete pads
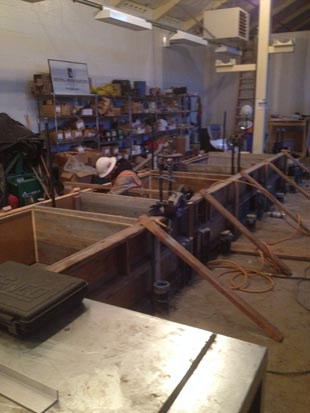
UV Disinfection pad form work
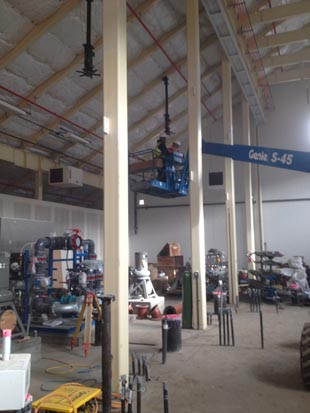
HVAC subcontractor installing destratification fans in Membrane Building
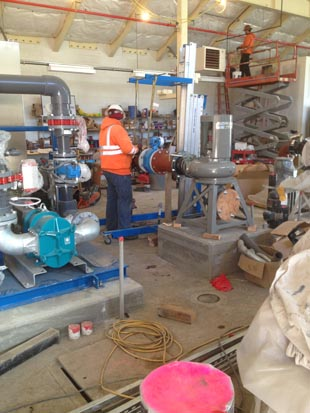
Installing RAS piping and flow meter at Membrane Building
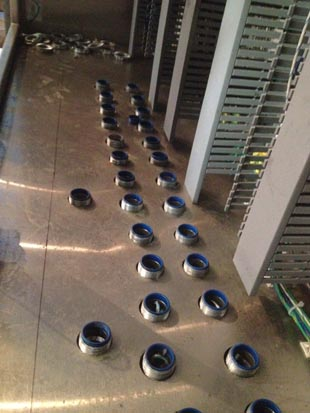
Conduits through bottom of Membrane Control Panel
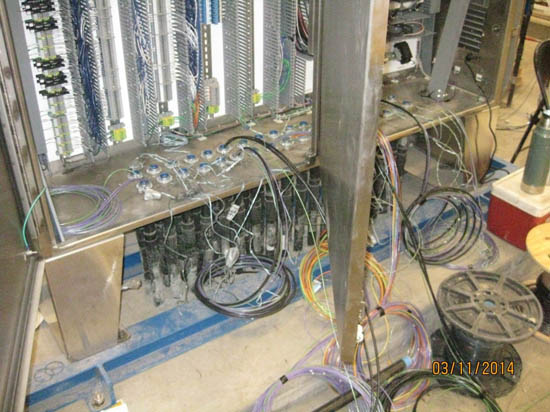
Field wiring of ZMOD panel for Membrane system
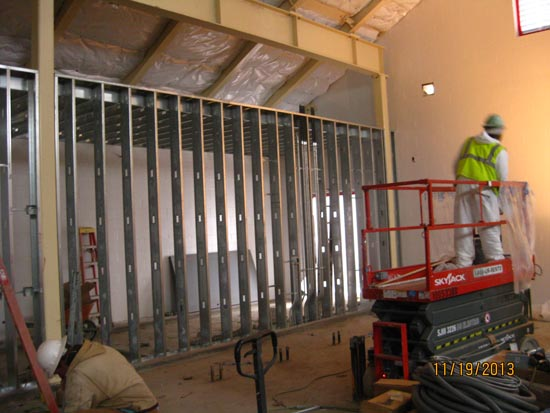
Building studs for electrical room at Membrane Building
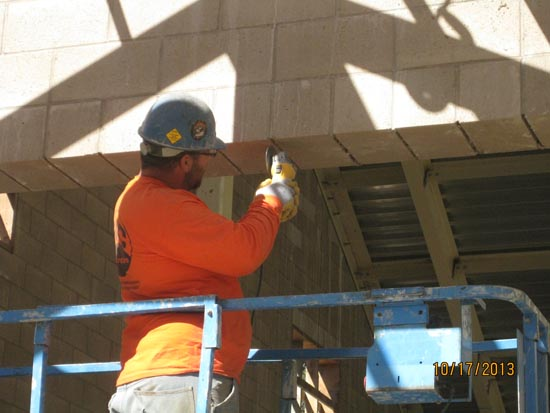
Drilling into epoxy bolts Membrane Building
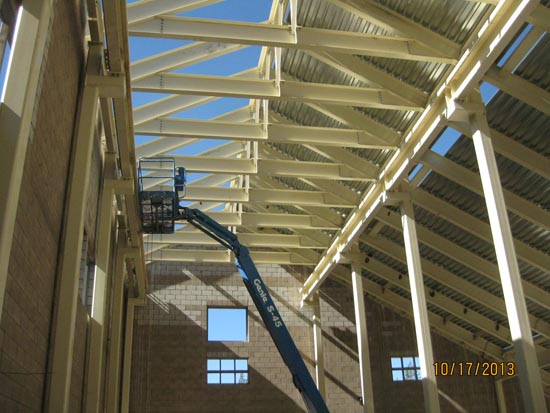
Installing roof pan decking at Membrane Building
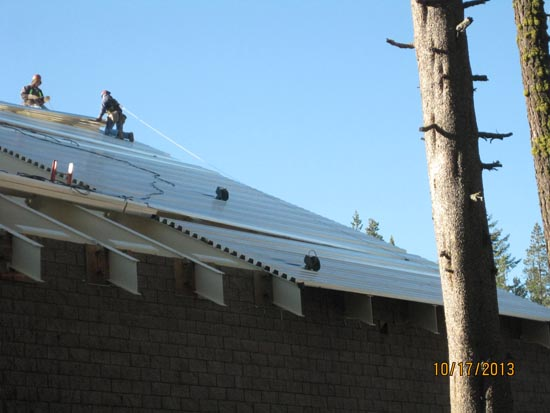
Installing roof pan decking at Membrane Building
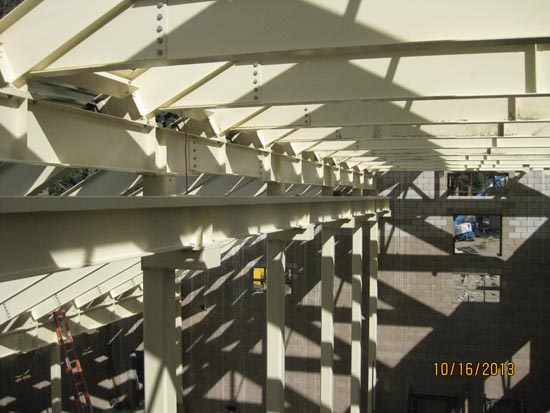
Steel at Membrane Building
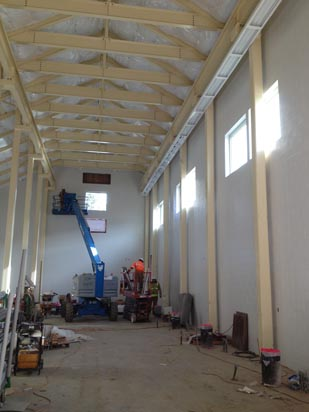
Interior of Membrane Building
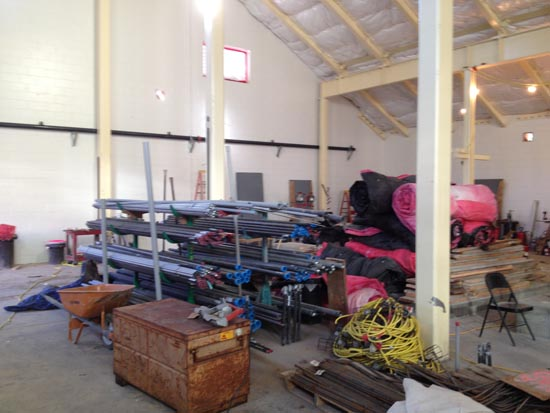
Interior at Membrane Building
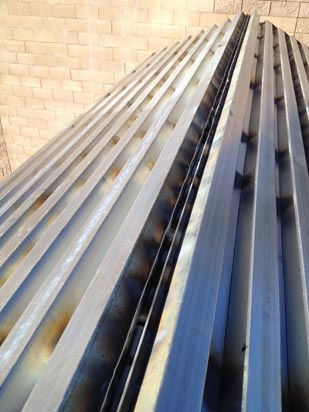
Who says construction can't be a work of art?
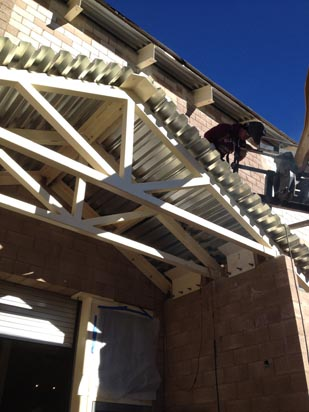
View of the roof decking at Membrane Building
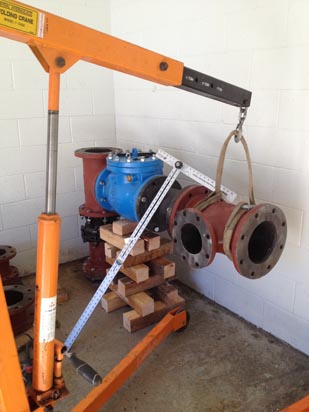
Assembling pipe at Membrane Building
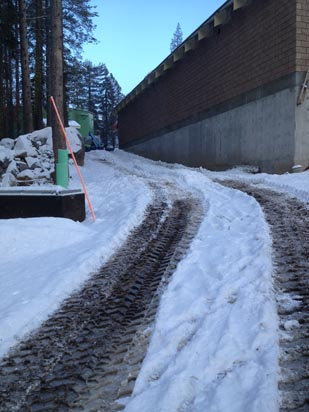
View from the north side of Membrane Building. The crew keeps working even in the snow.
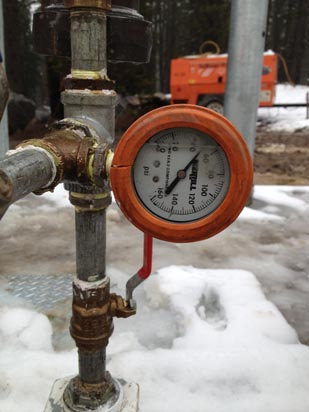
Testing the underground piping
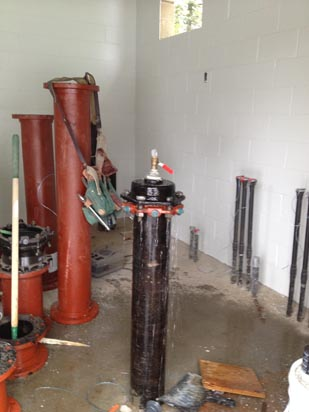
Pipe in Membrane Building
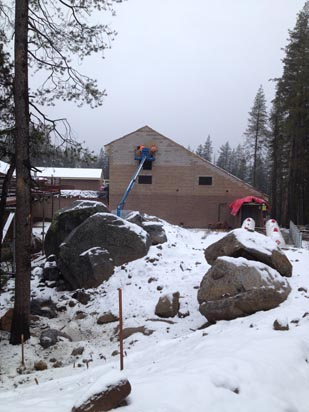
Setting windows at Membrane Building
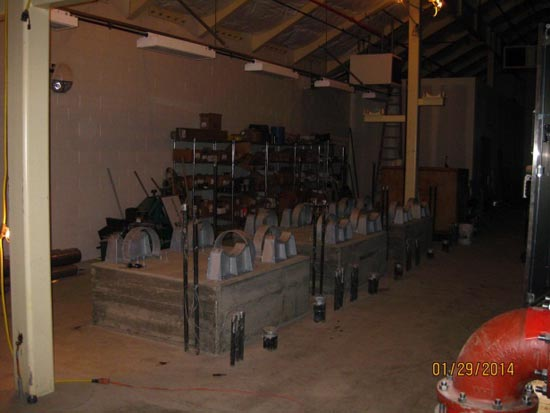
Laying out UV reactor supports at Membrane Building
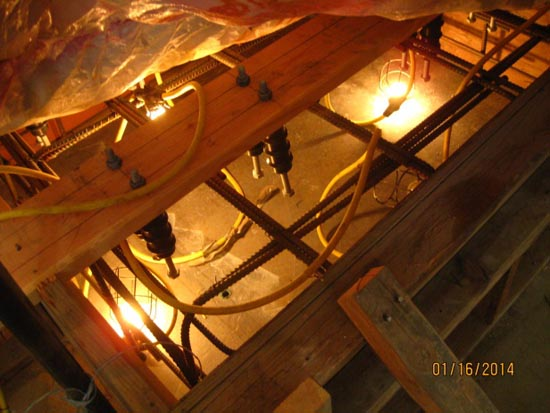
Preparing for UV pad concrete pour at Membrane Building
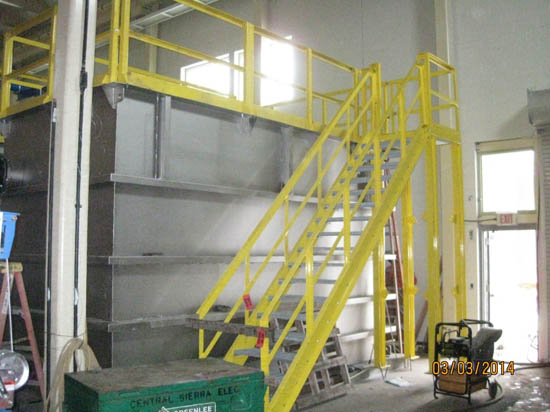
Stairway installation to Membrane reactors
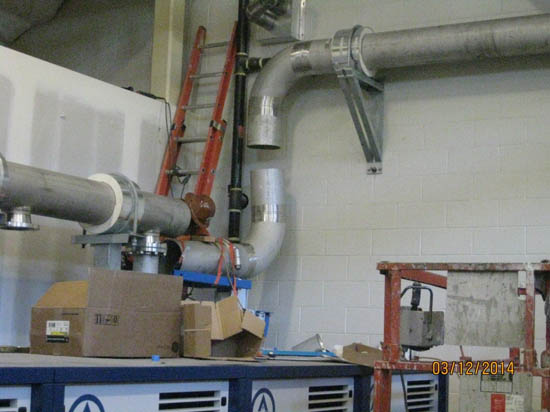
SST air piping installation at Membrane Building
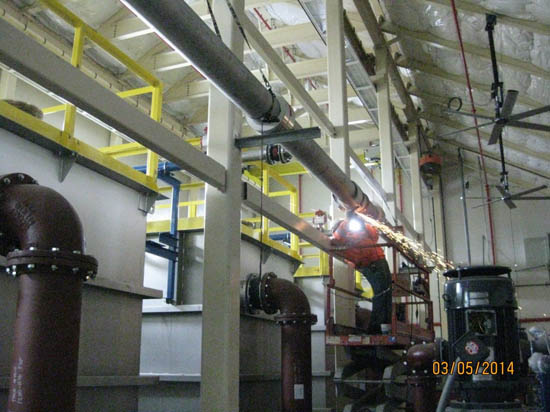
Installing SST air piping for reactor air at Membranes
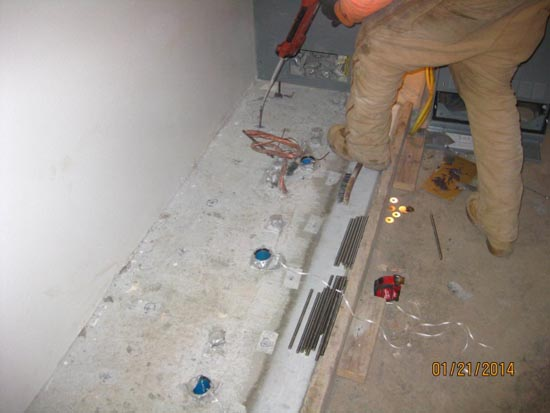
Installing SST epoxy anchors at Membrane Electrical Equipment
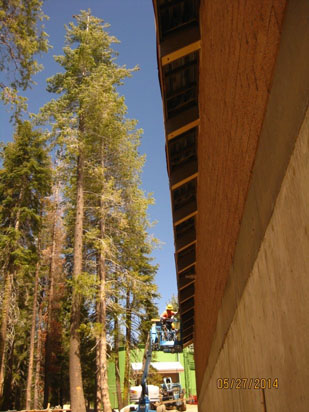
Starting beam enclosures and soffits at Membrane Building
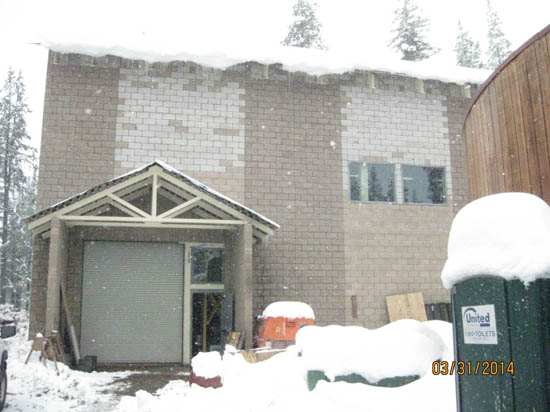
Snow at Membrane Building on March 31, 2014
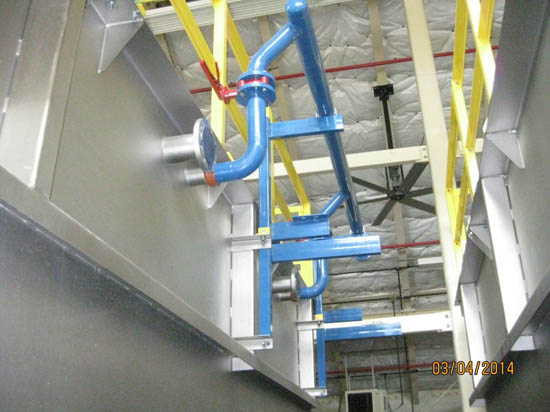
Stainless steel reactor basin with handrail and supports in Membrane Building
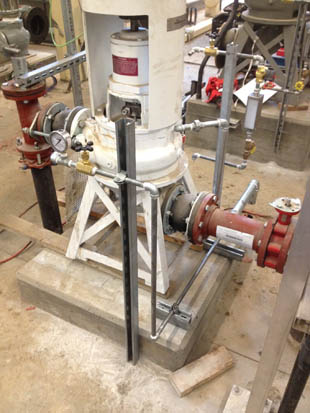
Double mechanical seal piping at foam spray pump
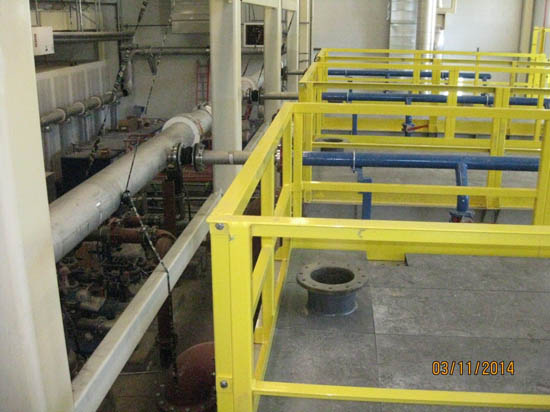
Top of Membrane treatment basins and SST air piping
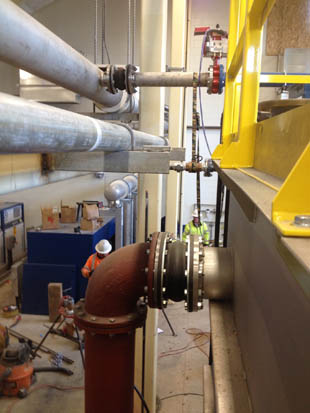
Overflow, foam spray, and aeration air pipelines at Membrane Building
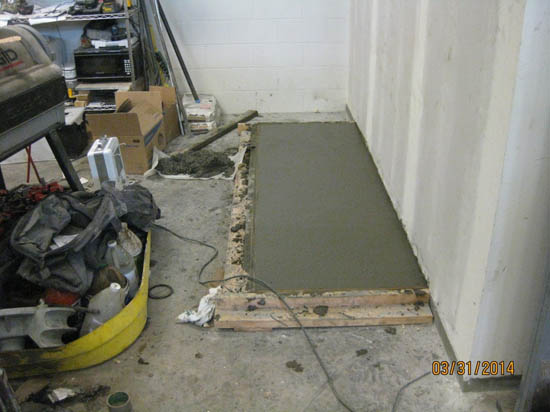
Concrete equipment pads for HVAC compressors
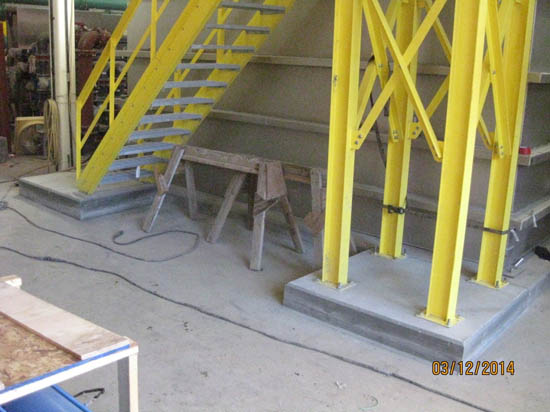
Concrete landing and stair pad for Membrane tanks
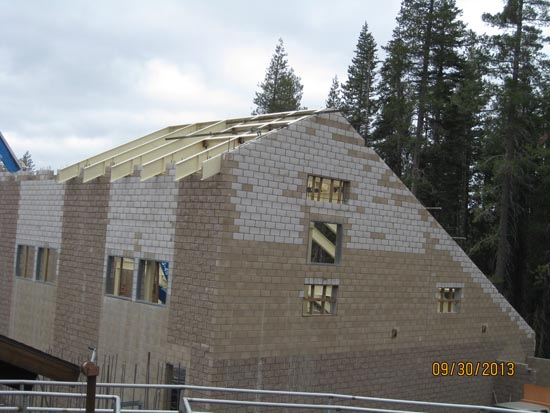
Structural steel on membrane building
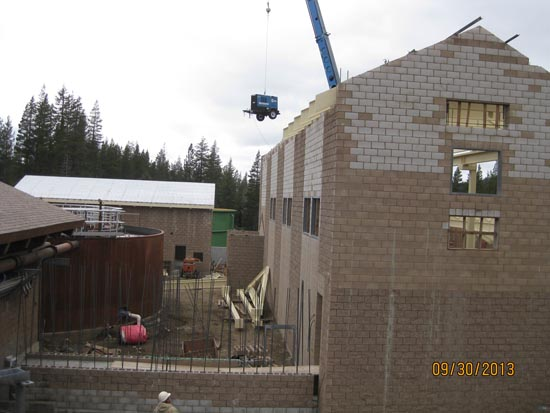
Walkway between membrane building and existing equalization tank
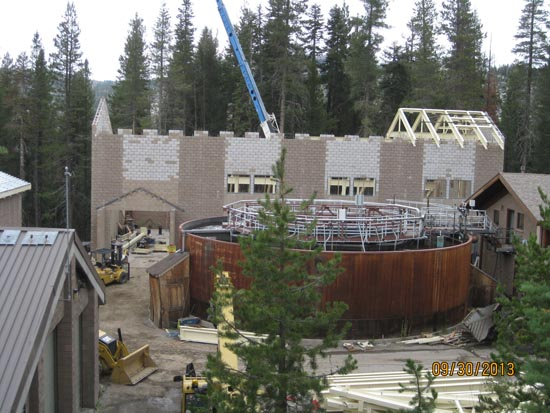
Membrane building
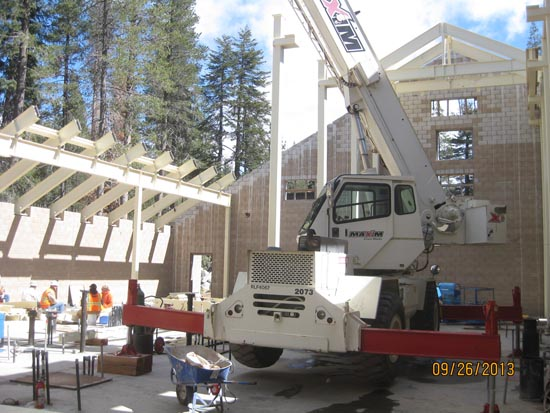
Recting steel at membrane building
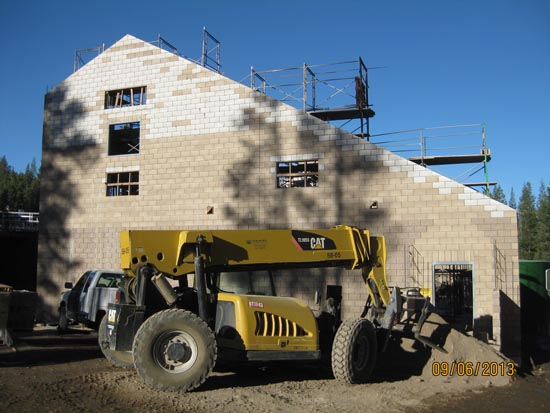
Membrane building
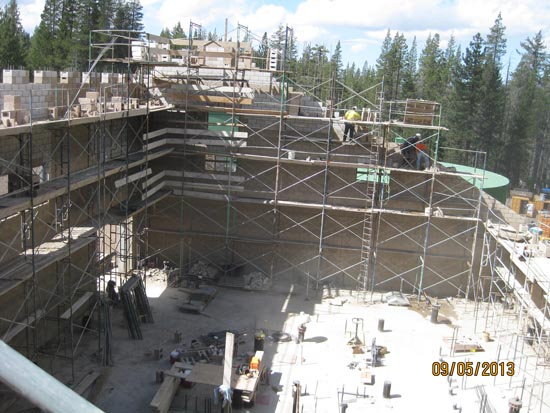
Membrane building
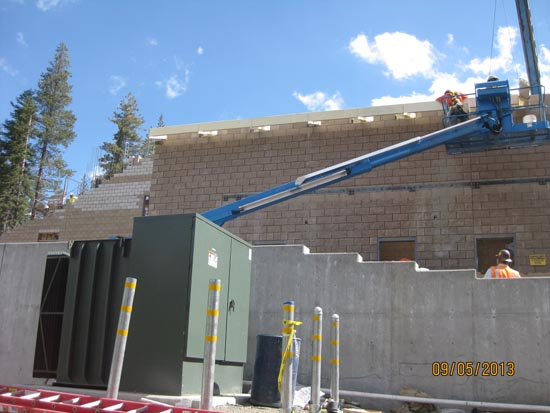
Structural Steel
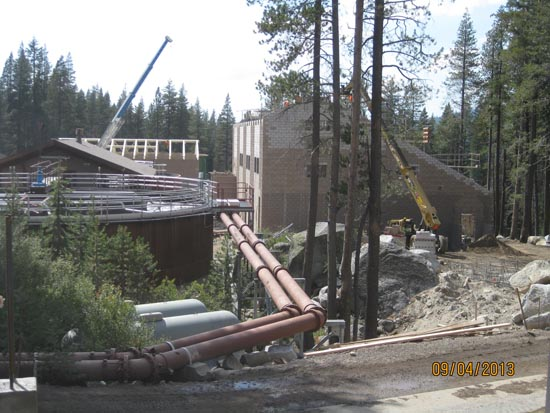
Chemical/electrical building and membrane building construction
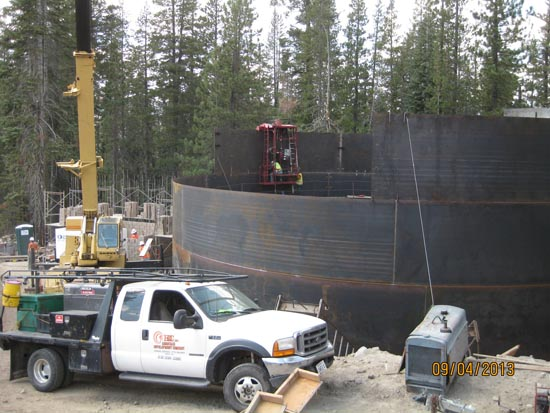
Fabricating new EQ Basin #2
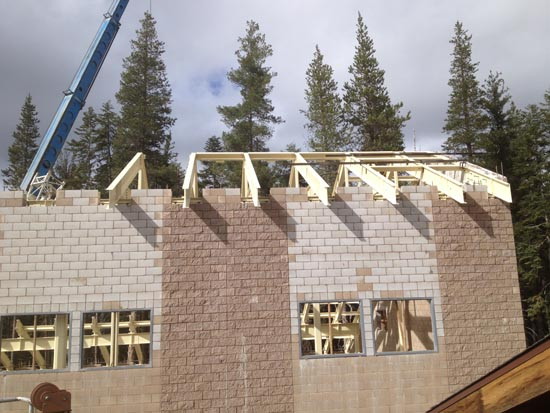
Beam placement at Membrane Building
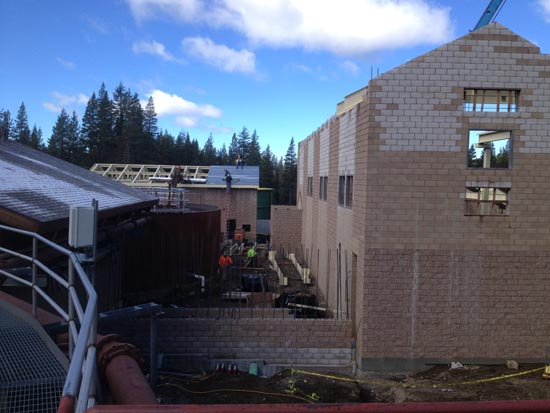
Membrane and C/E building
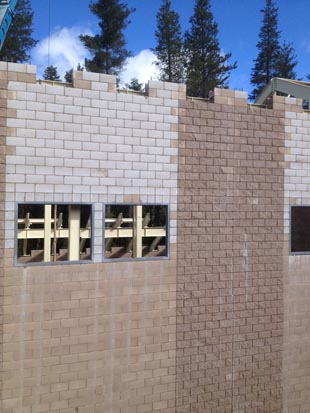
South wall of membrane building
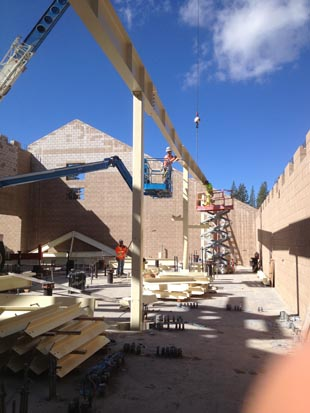
Structural steel at membrane building
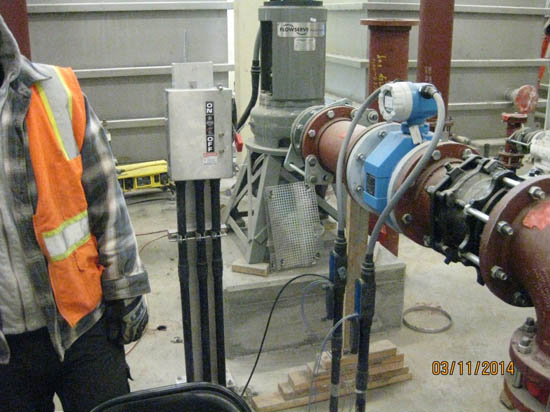
Disconnecting the flow meter for RAS pump and piping at Membrane Building
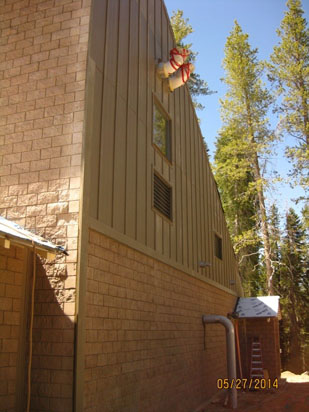
Hardie board siding with battens at Membrane Building
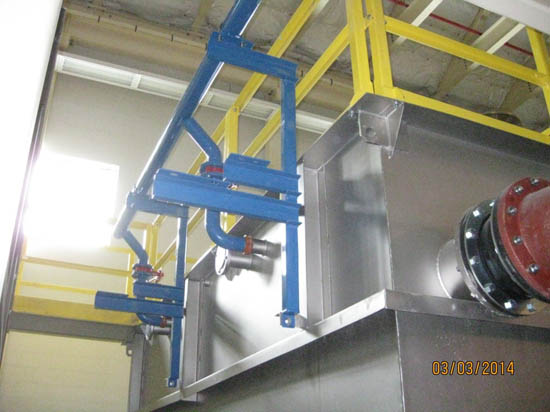
GE factory pipe racks for Membrane reactor tanks
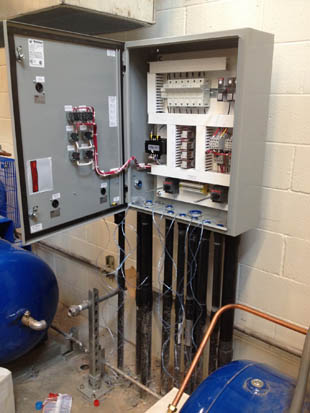
Membrane instrument air compressor control panel
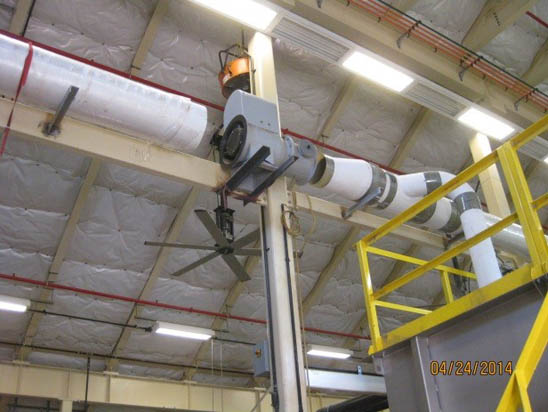
Exhaust fan for venting air from Membrane tanks
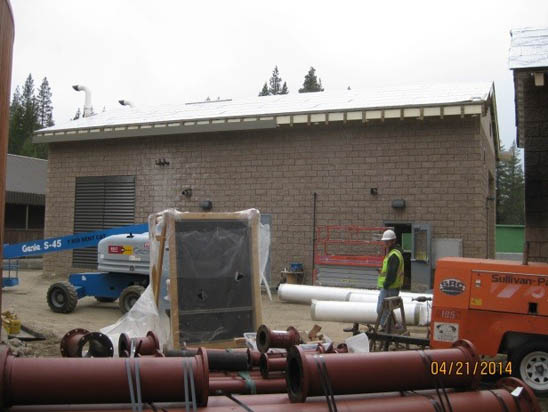
Chemical equipment skid for Membrane tank
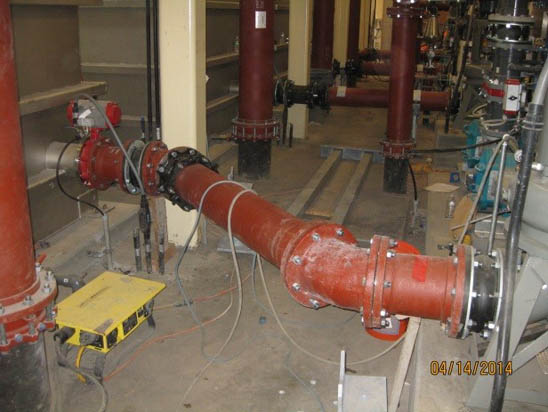
RAS pumps with piping complete to Membrane tanks
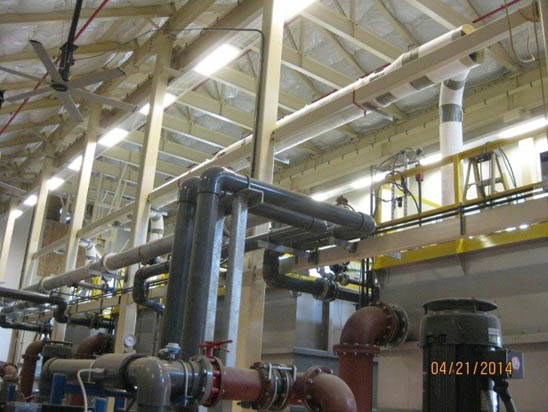
The installation of permeate piping at Membrane Building.
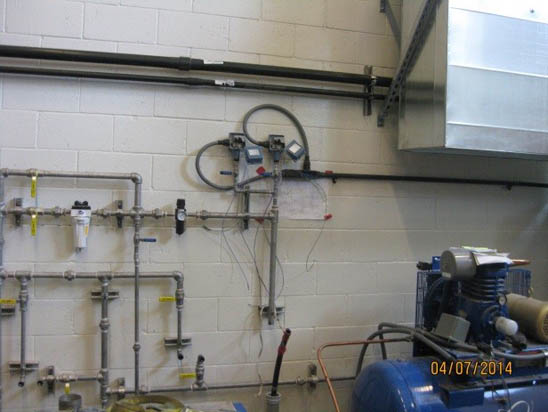
Instrument air system on east wall of Membrane Building
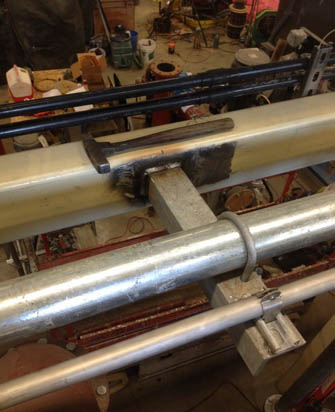
Foam spray and air piping north of Membrane tanks
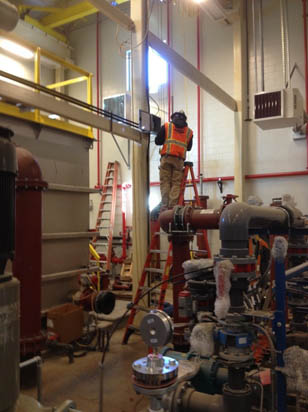
Installing de-stratification fan controllers at Membrane Building
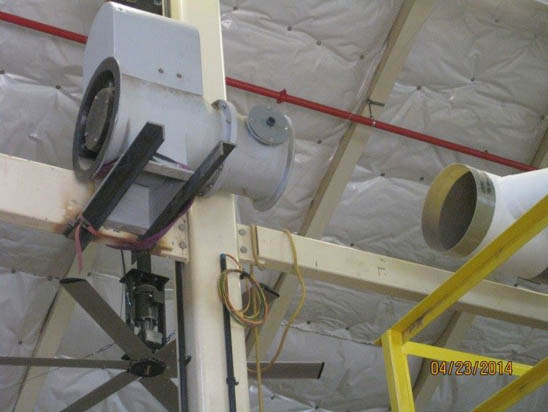
Membrane unit vent exhaust at Membrane Building
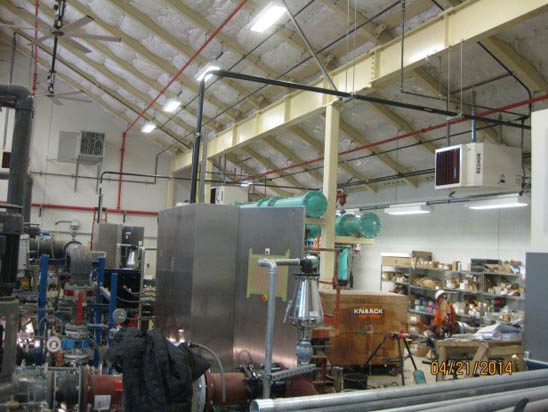
Electrical control panels and conduits for membranes @ Membrane Building
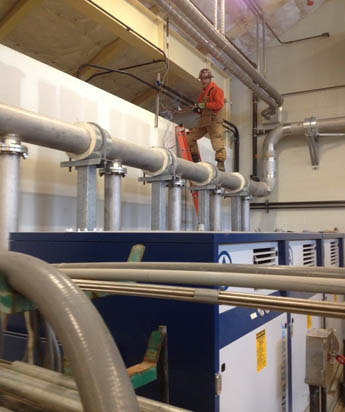
Conduit install about Electrical Room at Membrane Building
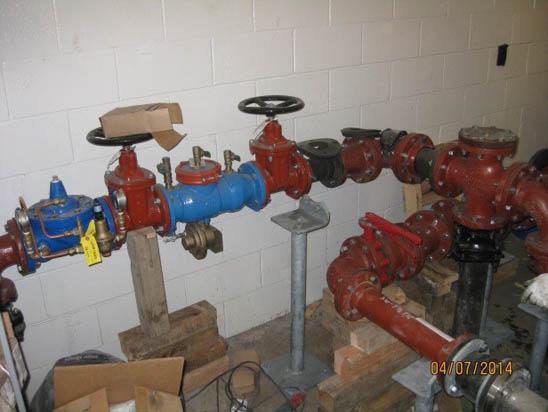
2 Water backup supply and 3 water piping at Membrane Building
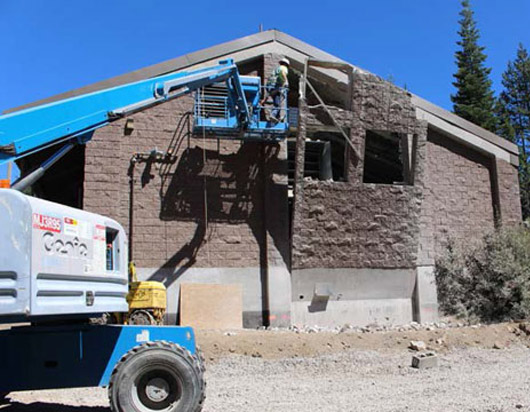
The demolition of the wast wall of the Advance Treatment Building in order to place a new rollup door.
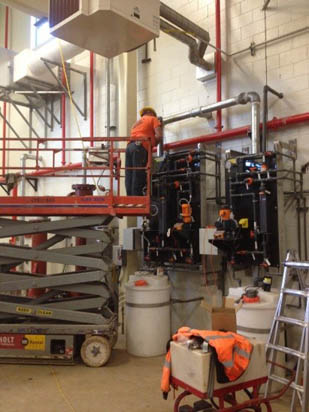
Chemical Tank for the Membrane backwash process.
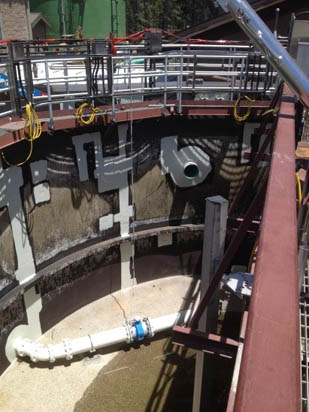
Reactor #2 Tank recycles piping between the aerobic and anoxic zones.
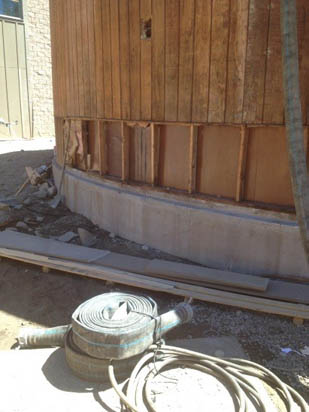
Reactor #2 Tank has fixed pinholes and the tank is no longer leaking.
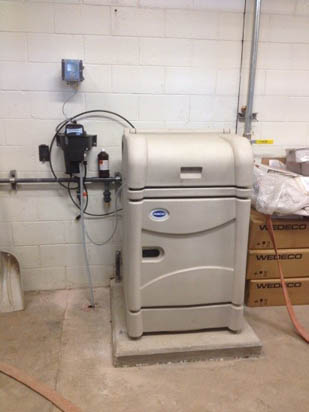
meter07232014Effluent automatic sampler and turbidity meter located in the Membrane Building
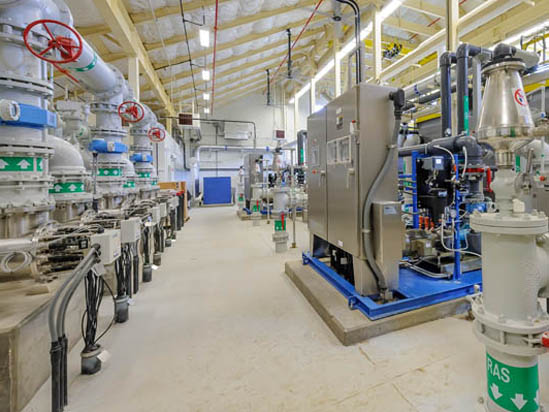
Boilers and recirculation pumps help keep influent at a constant temperature.
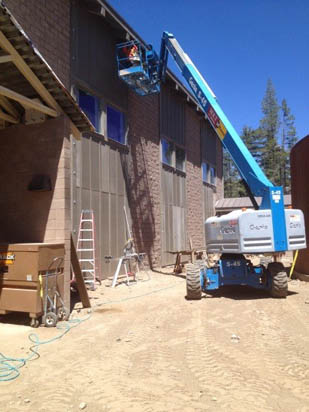
South face of the Membrane Building
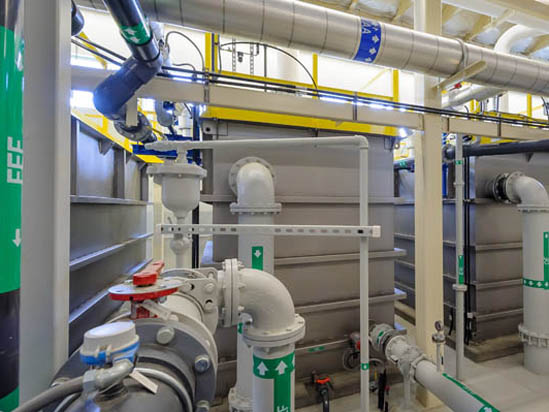
Using pumps, effluent is pushed through membranes which filter out final particles
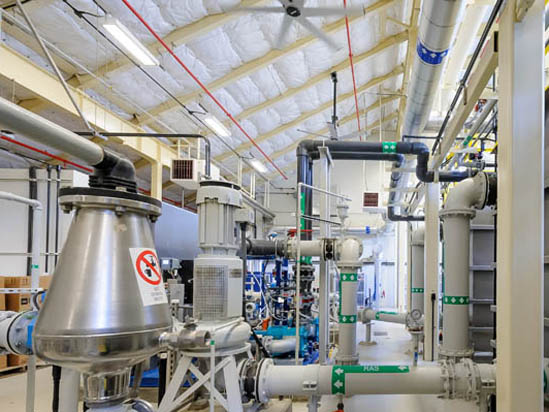
MBR process and piping
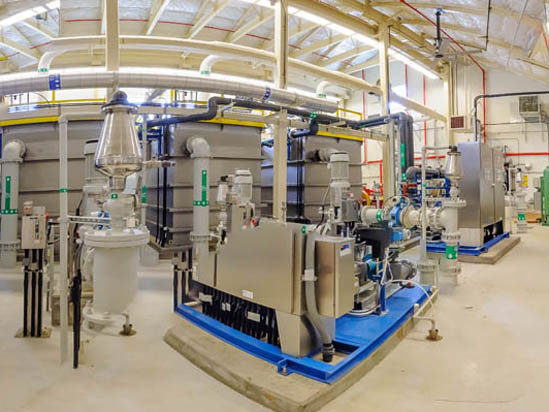
MBR treatment allows for the greatest removal of nitrate and ammonia during the treatment process
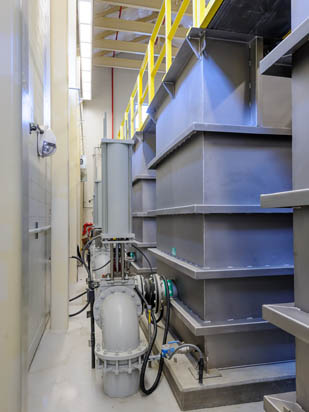
Membrane filters replaced previously used clarifiers
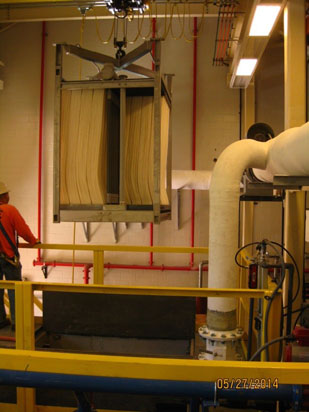
Hoisting Membrane cassette using 5 ton district crane.
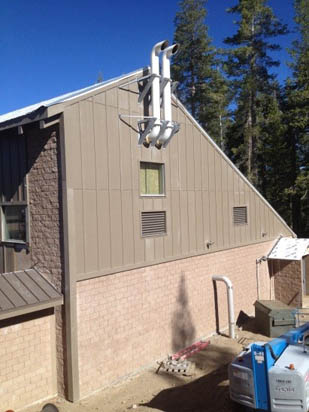
Membrane Building fascia with heat exchanger exhaust pipes
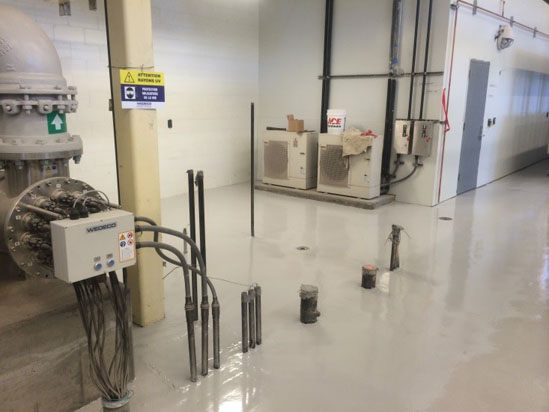
The floor coating of the Membrane Building.
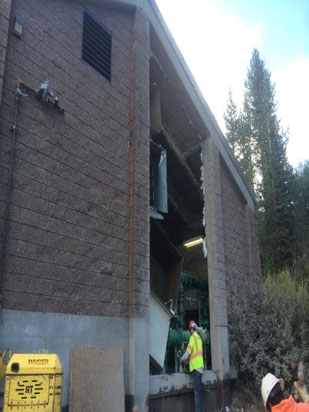
The view of the Advance Treatment Building west facing wall after block removal.
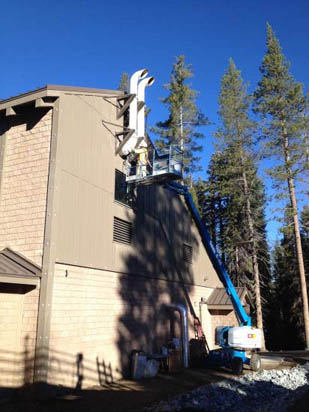
Farr West Insulation has begun work on the exhaust pipes at the MEB. They have already completed insulation on CEB's exhaust pipes.
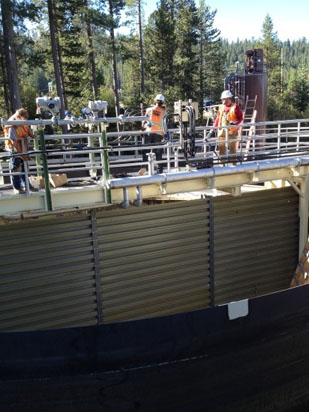
The modifications, equipment and electrical installs on Reactor Tank #1.
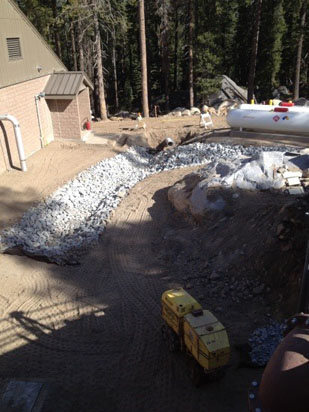
A rip rap lined ditch located on the east side of the Membrane Equipment Building.
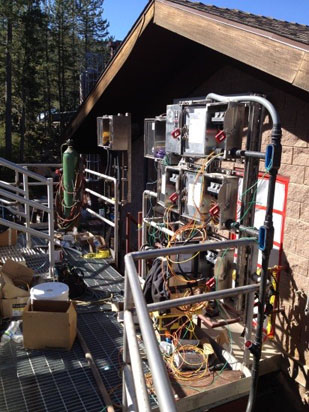
The view looking at the Reactor Tank #1 disconnects for all the mixers and wall pump.
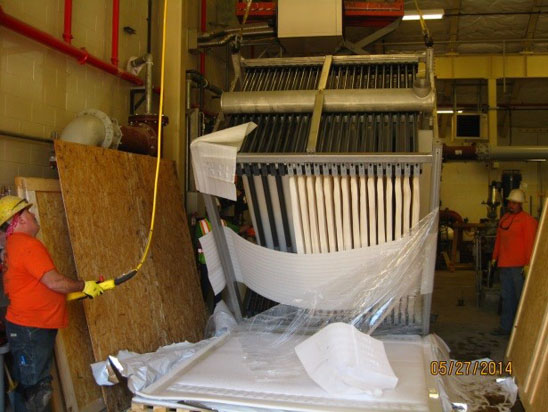
The use of crane during the un-crating of the Membrane cassettes.
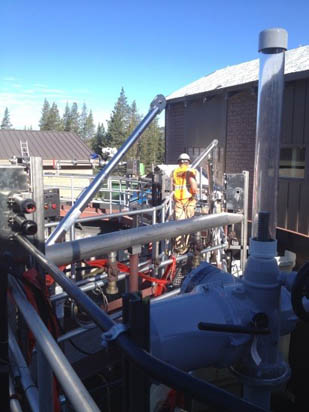
cranes07232014Reactor #2 davit cranes for mixers and pump
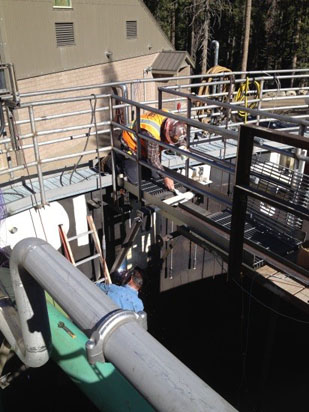
Reaction Tank #1 catwalk modifications.
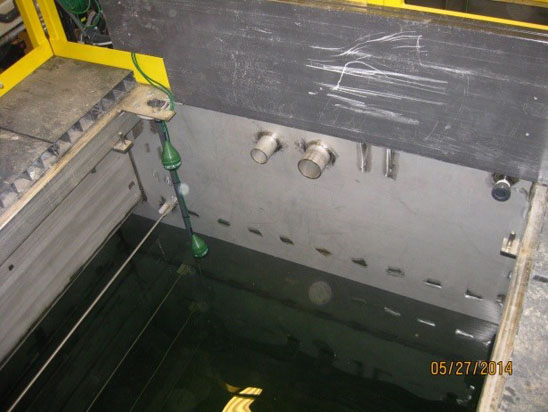
Interior of Membrane Tank before setting cassettes
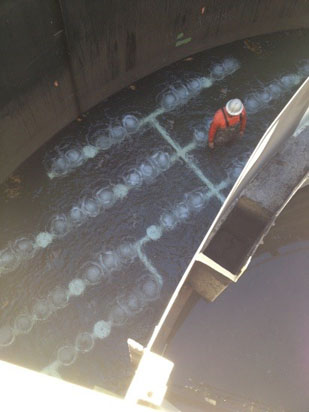
A fine bubble diffuser installed in Reactor Tank #1.
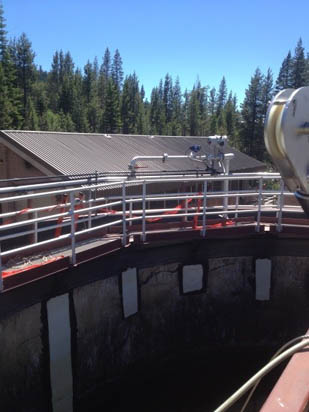
Reactor #2 Tank modified the air piping for the fine bubble diffuser system.
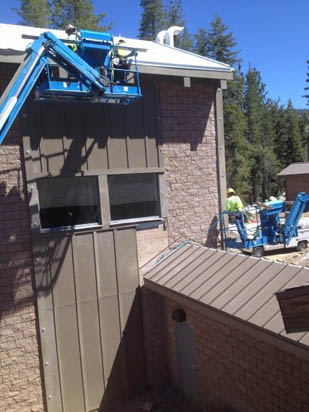
Membrane Building and breezeway to the Equipment Building roofing
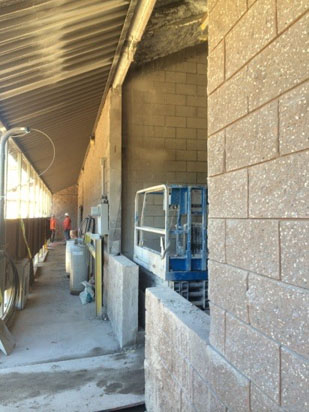
CMU block removal at the Advance Treatment Building north wall.
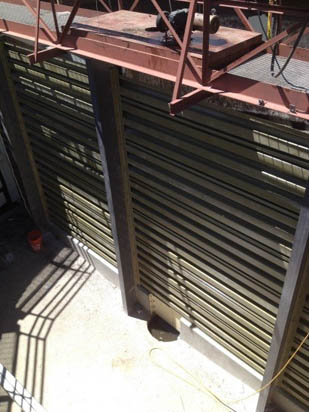
Fiberglass reinforced baffles to split anoxic zones for the Reactor #2 Tank.
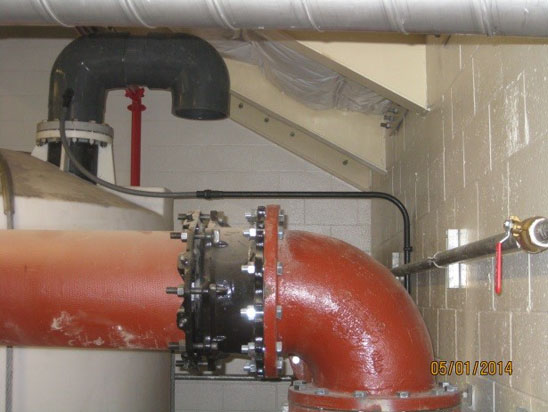
Backpulse tank vent at north west of Membrane Building
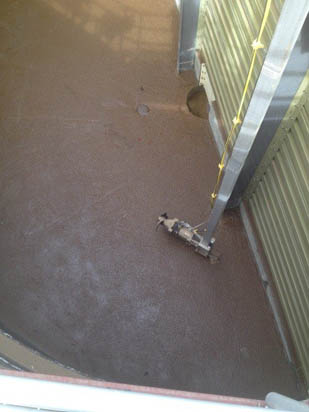
Mixer in the anoxic zone of the Reactor #2 Tank
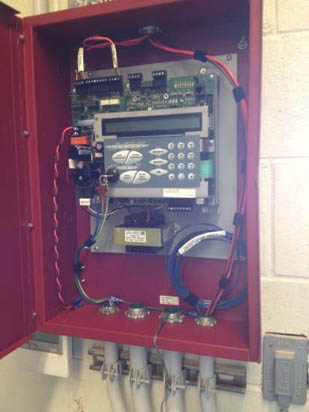
Central Sierra Electrical Subcontractor (Costco) installed the fire alarm system cabinet in the Membrane Equipment Building electrical room.
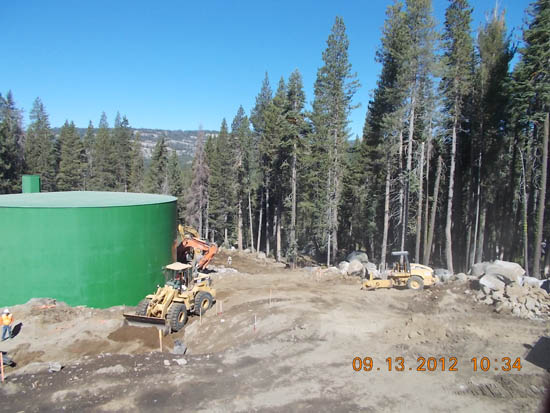
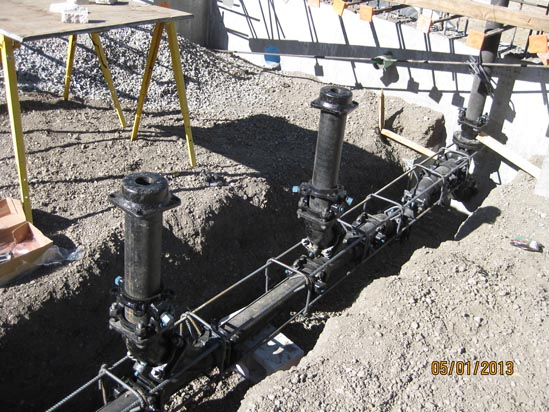
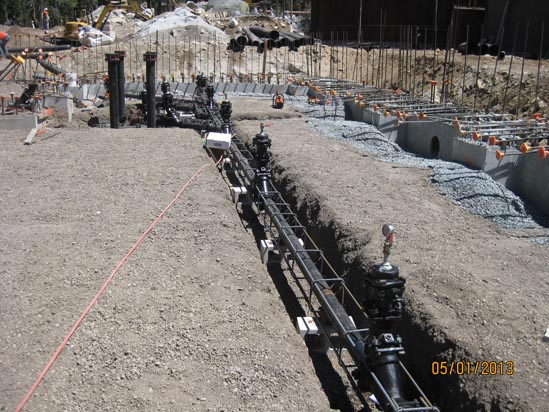
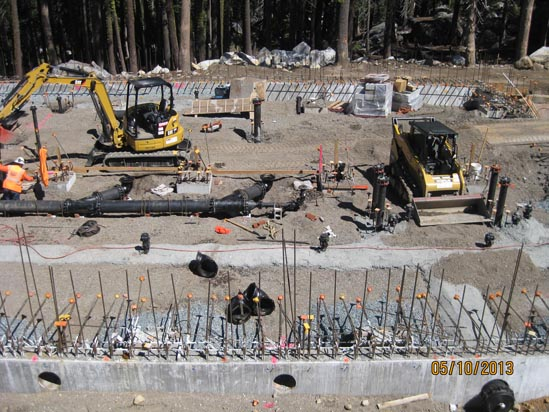
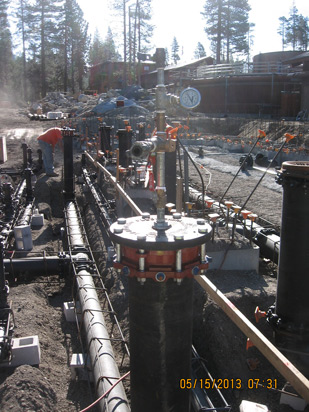
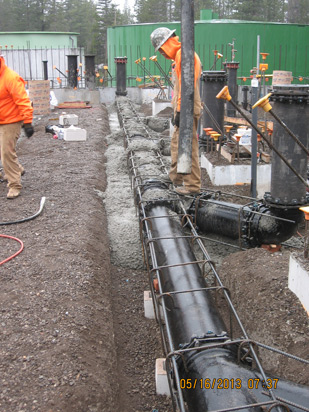
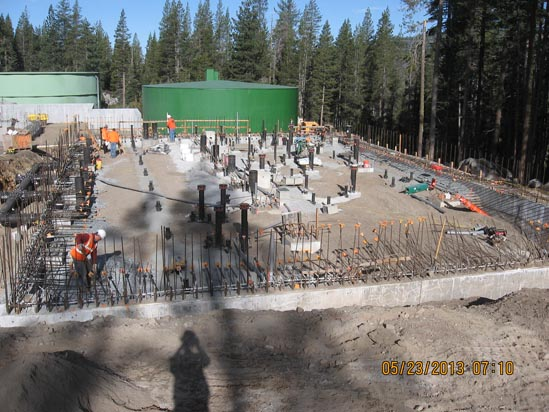
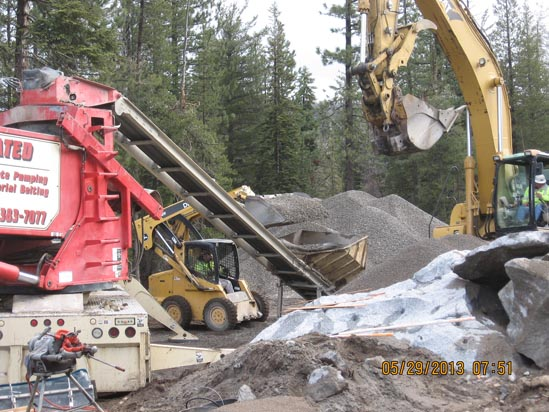
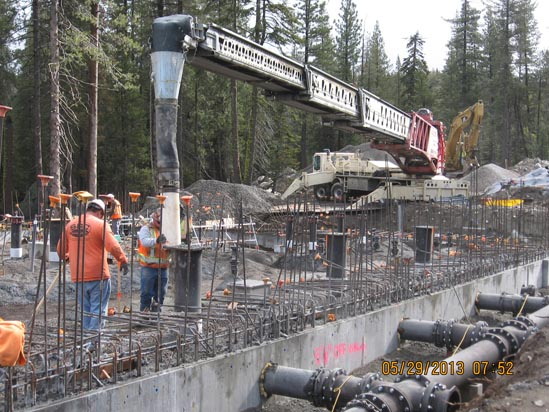
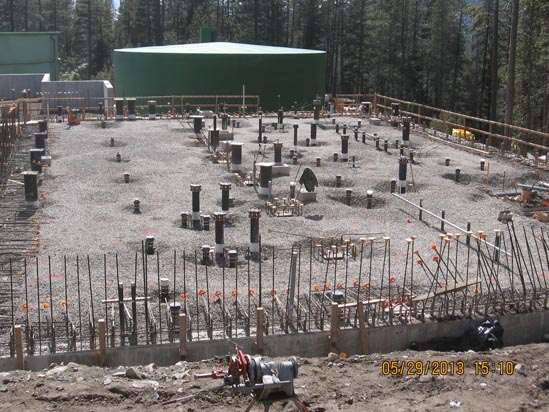
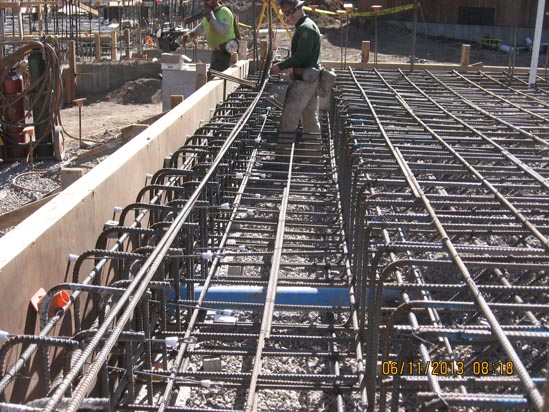
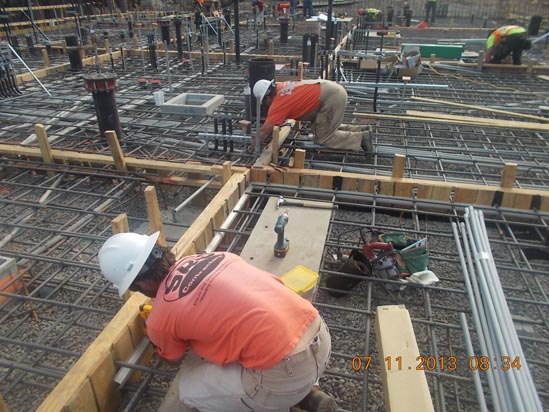
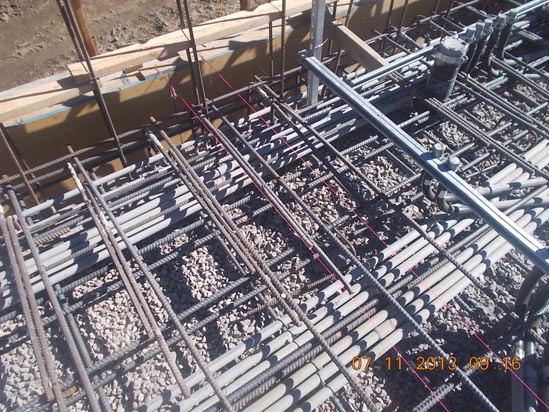
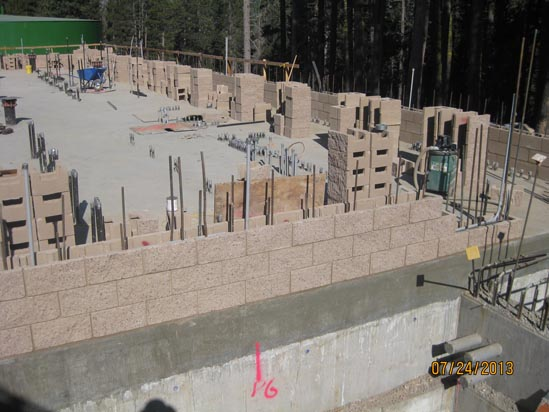
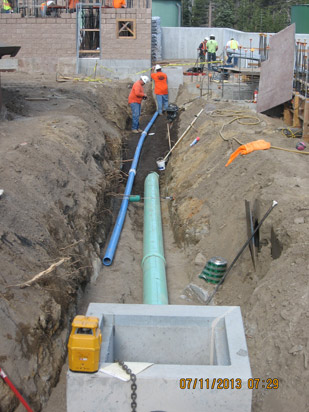
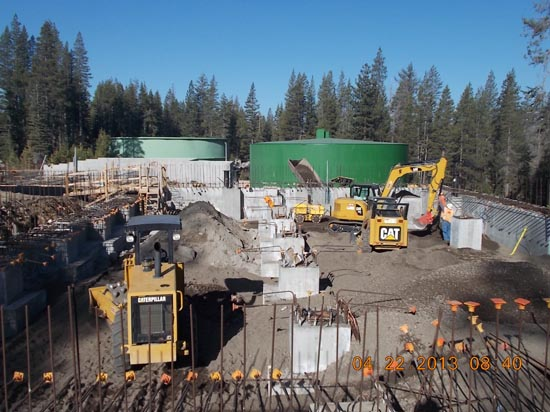
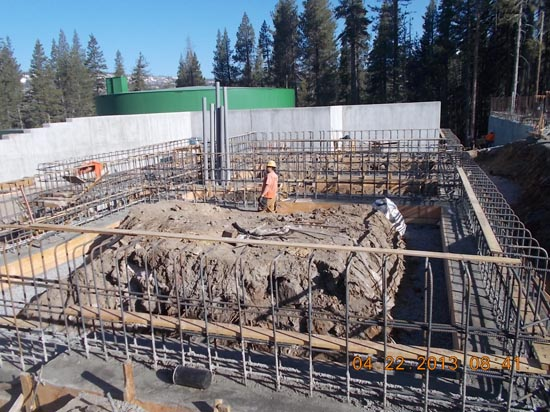
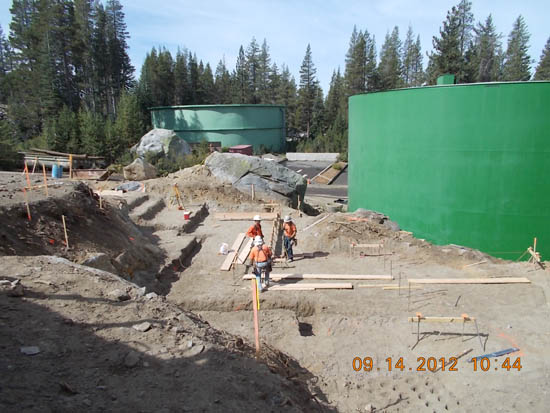
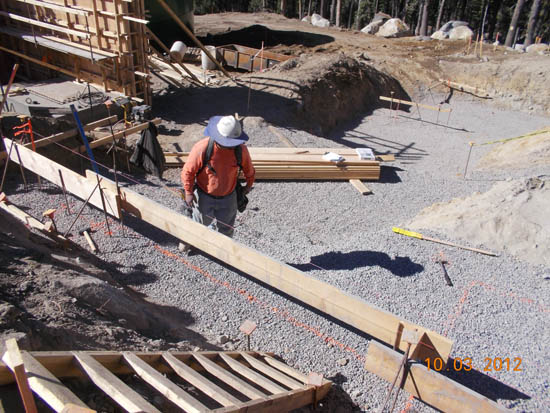
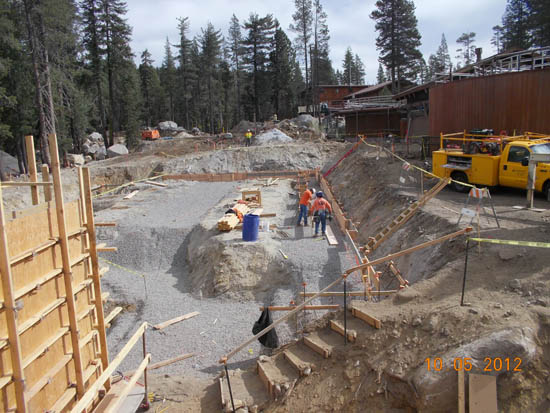
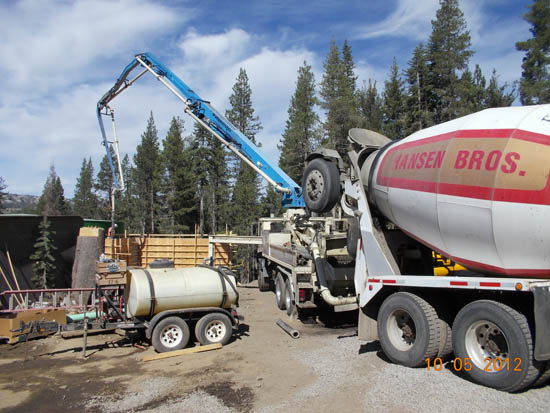
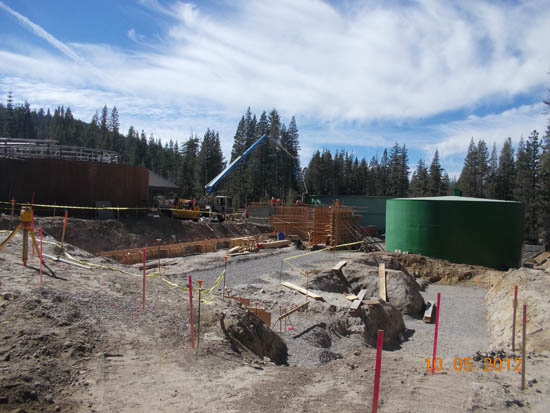
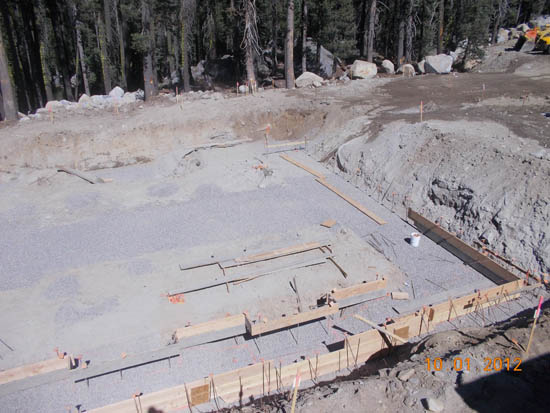
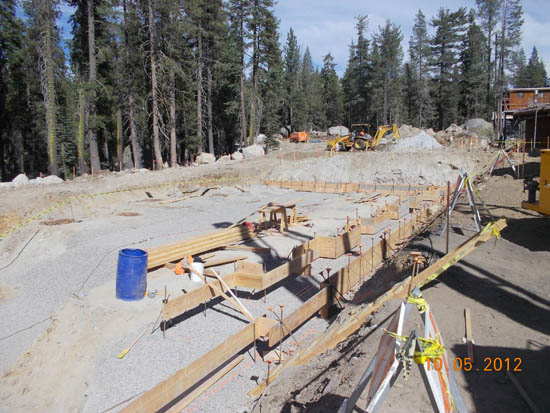
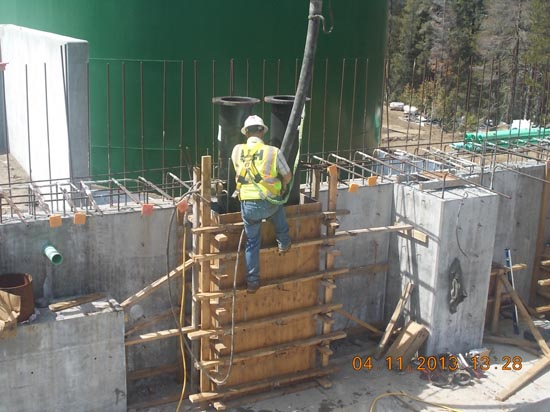
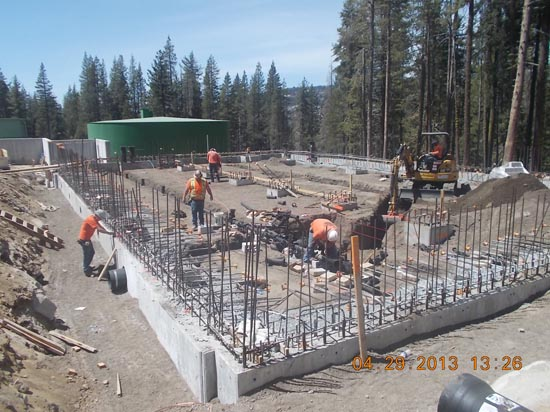
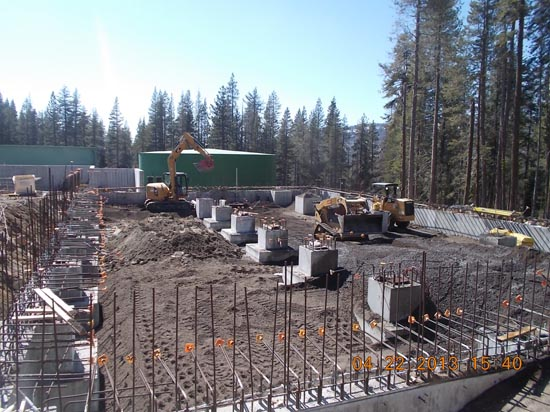
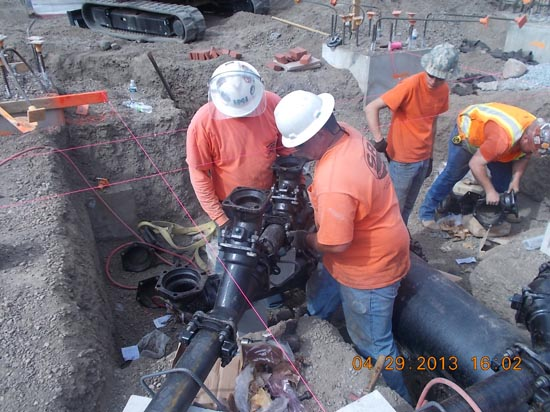
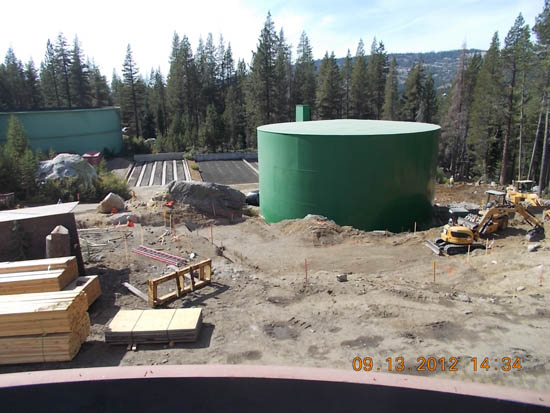
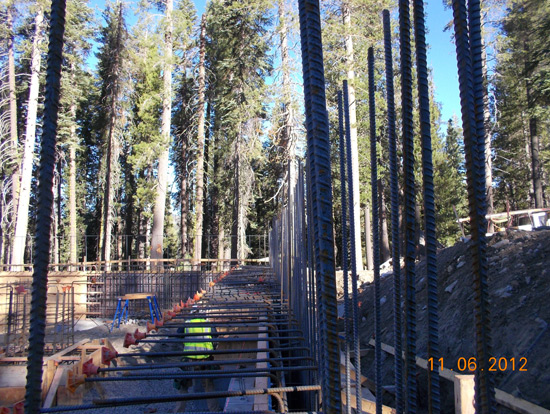
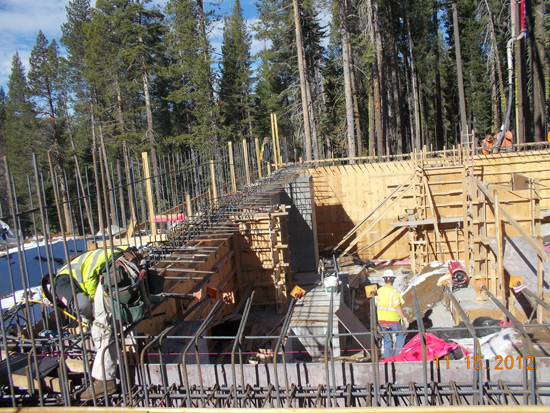
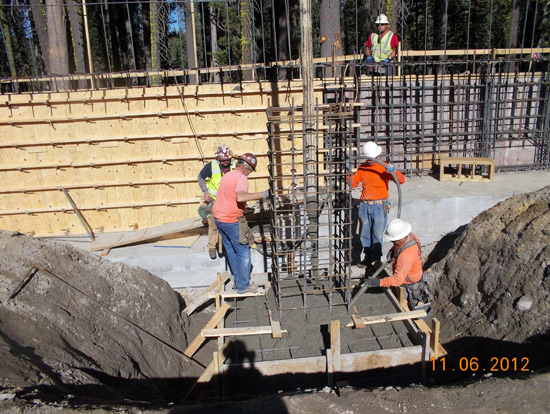
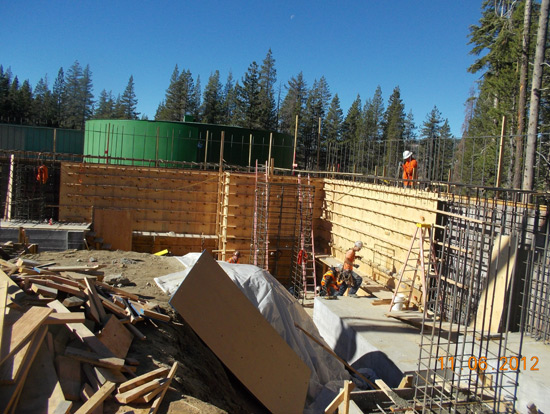
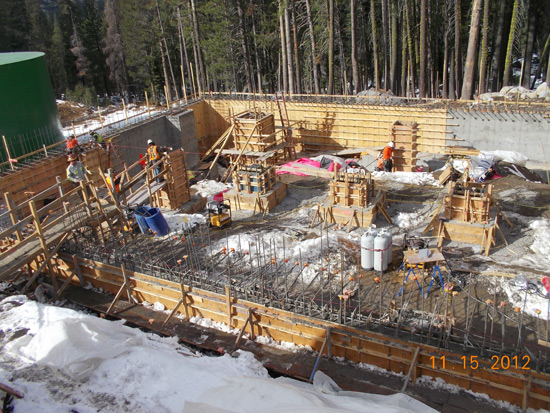
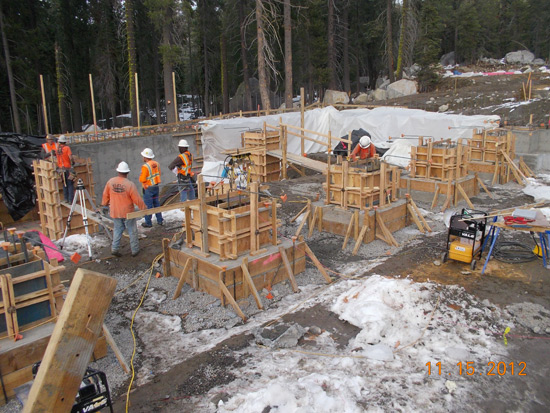
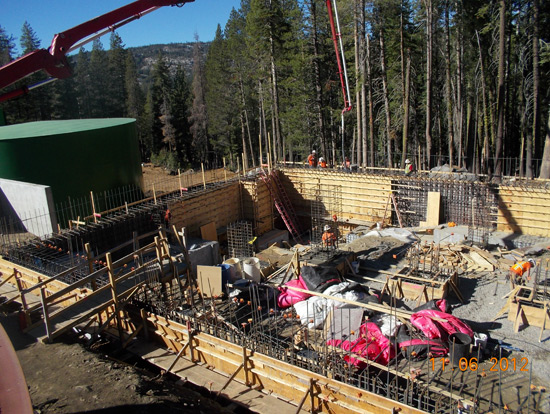
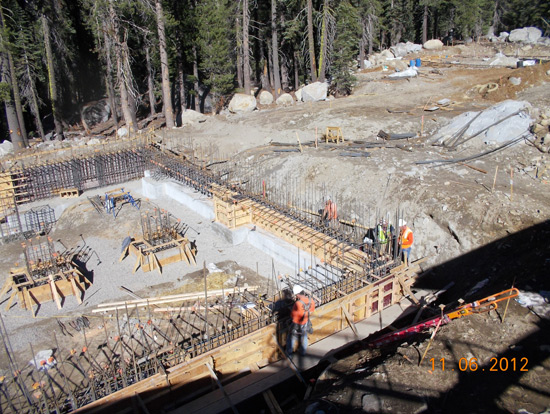
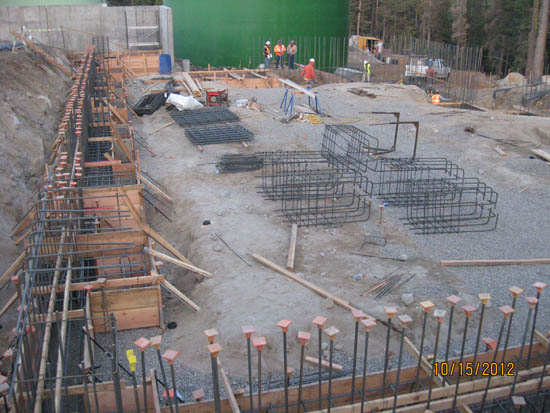
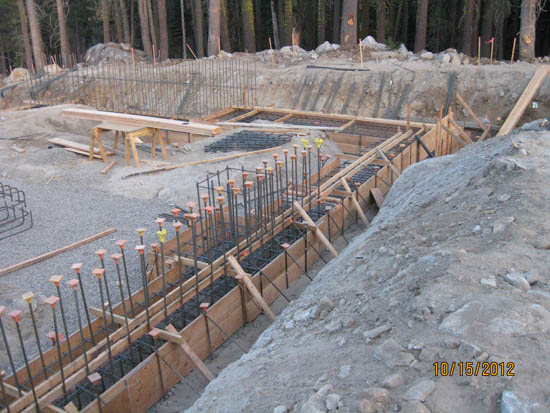
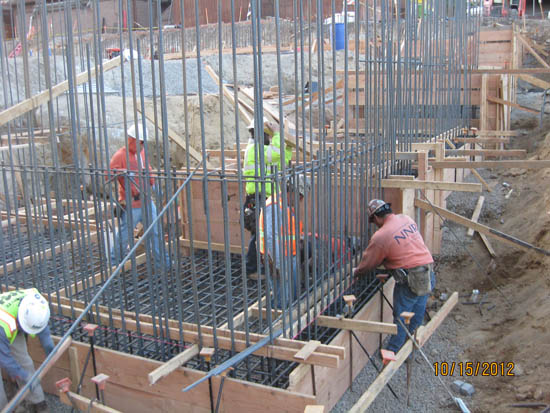
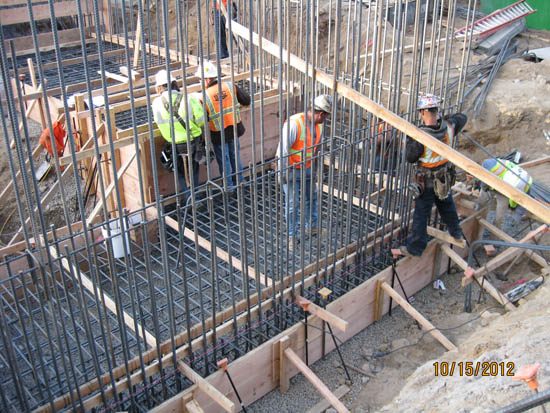
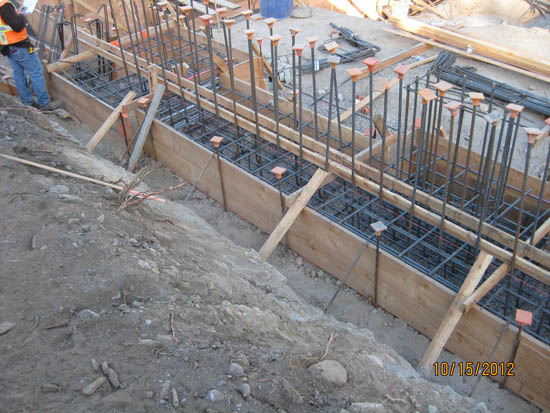
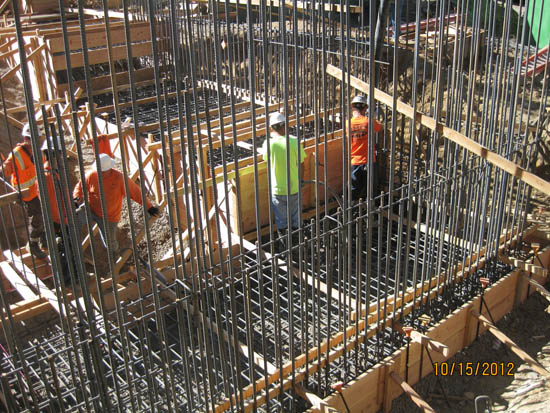
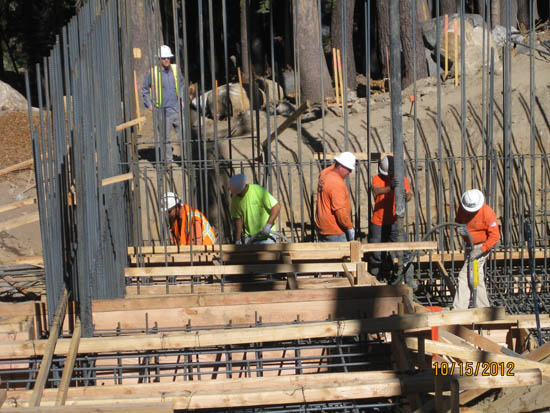
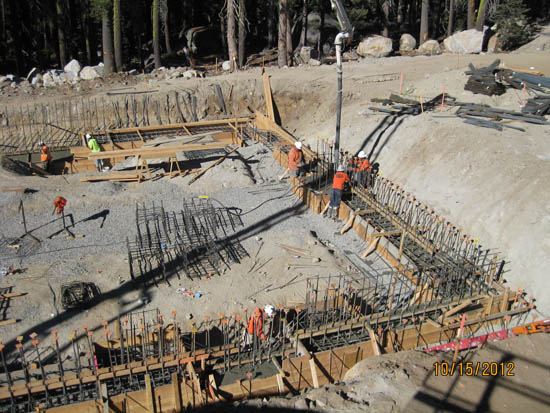
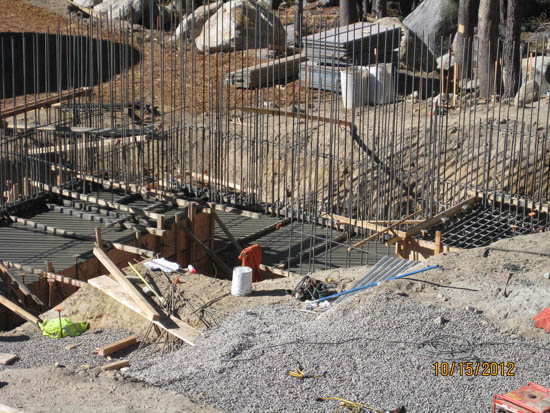
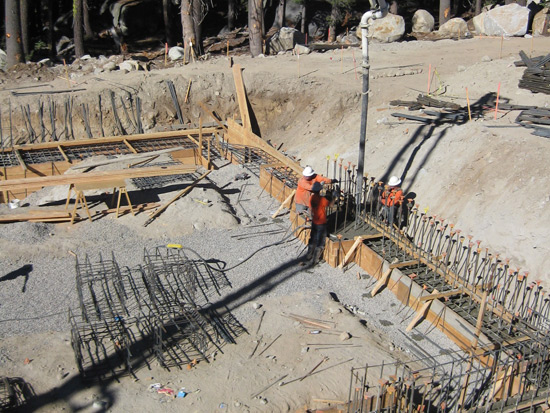
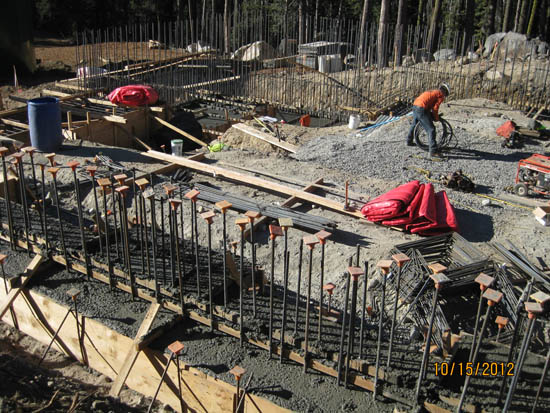
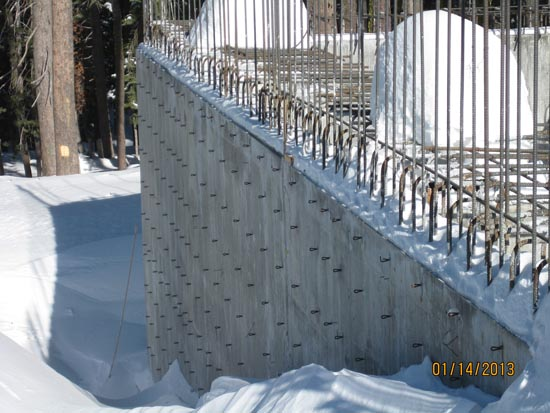
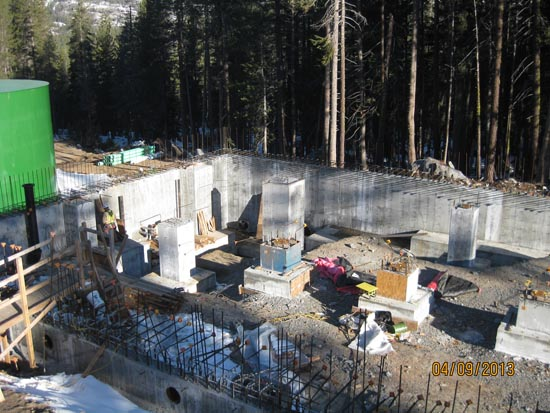
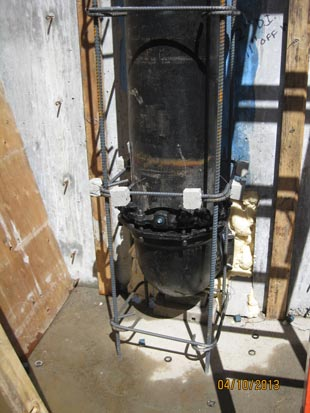
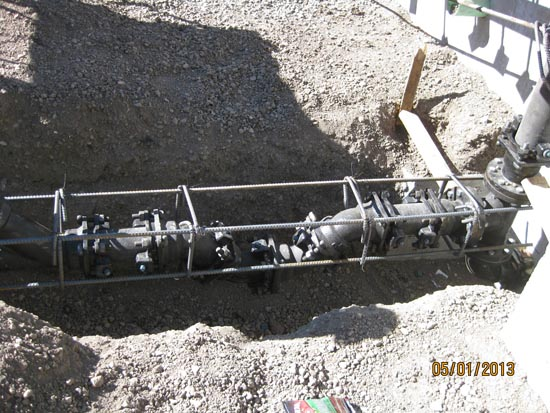

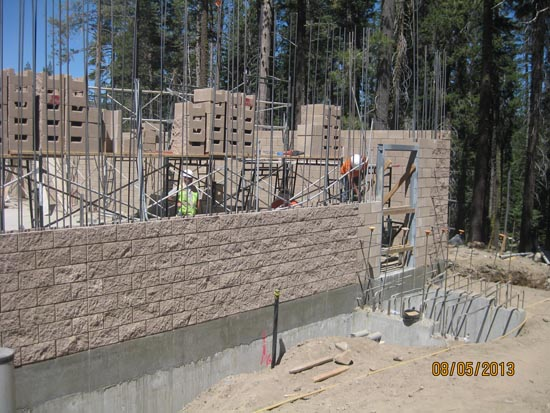
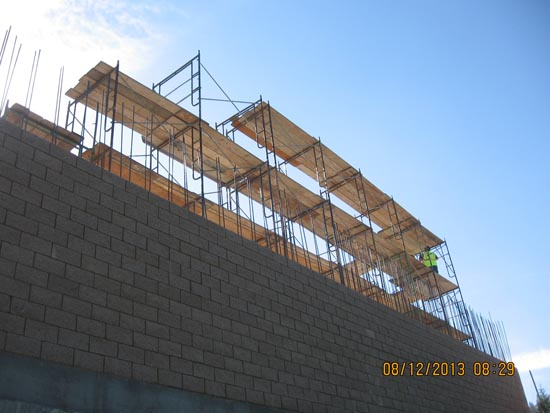
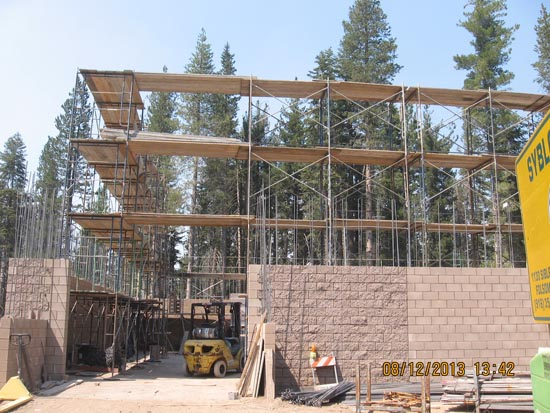
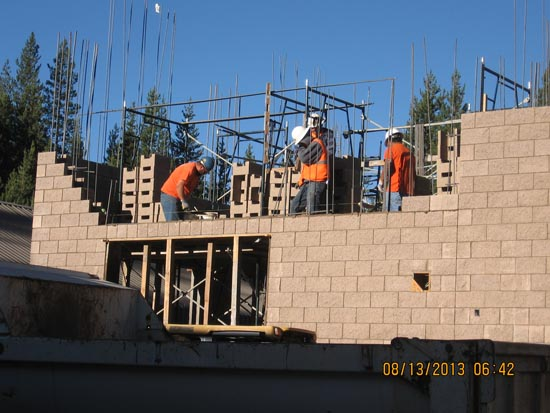
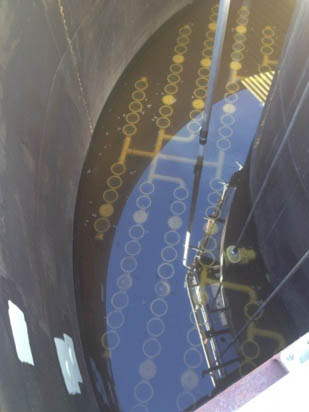
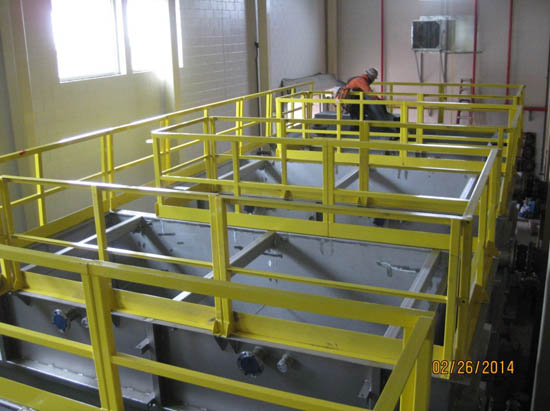
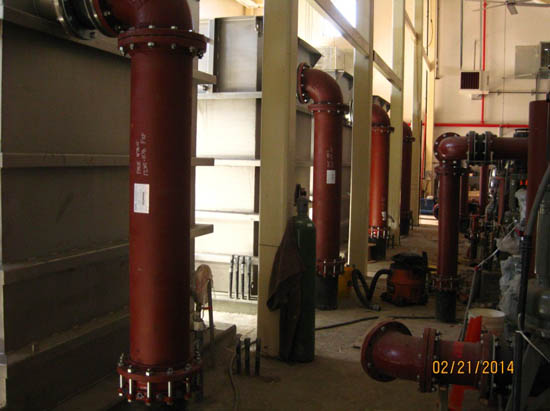
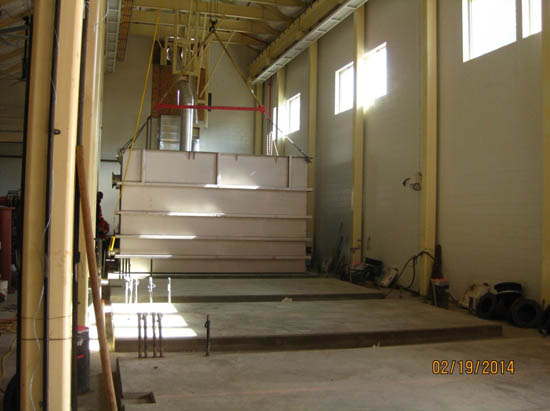
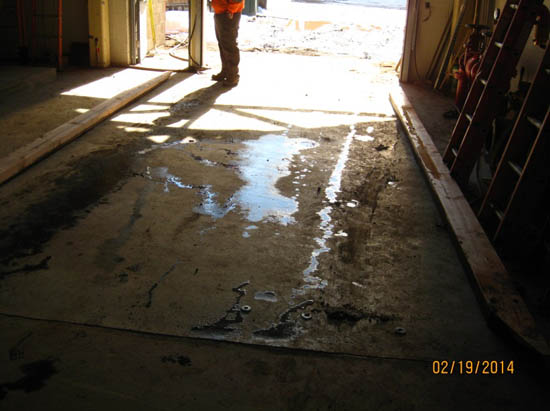
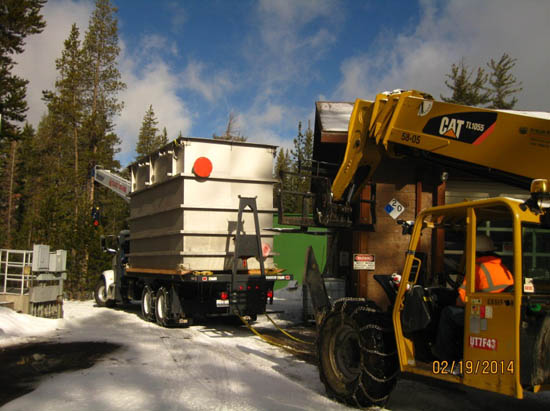
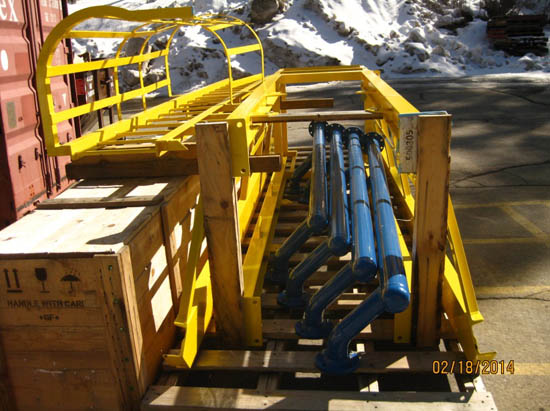
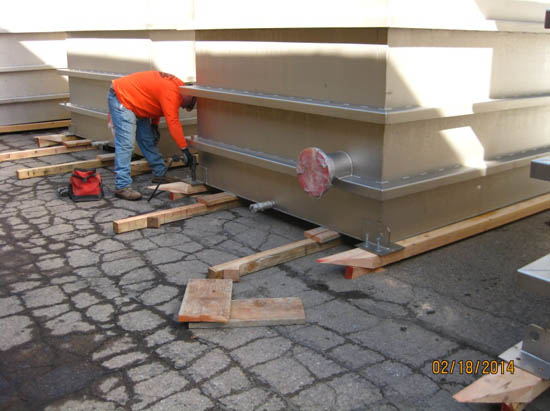
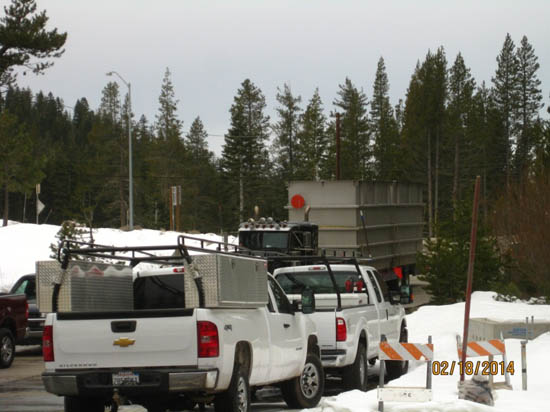
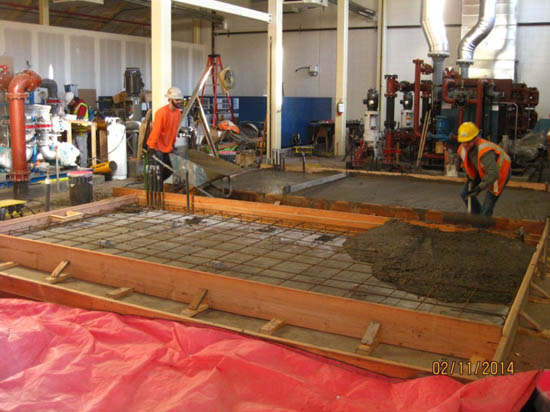

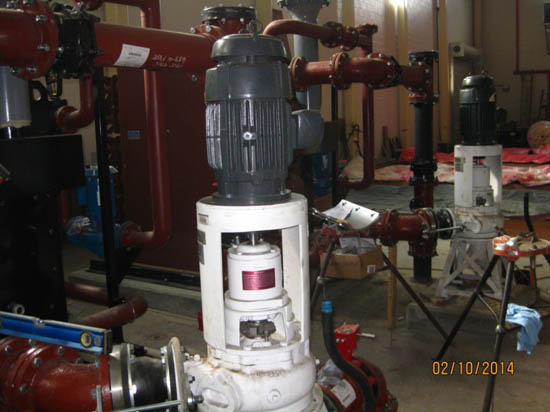
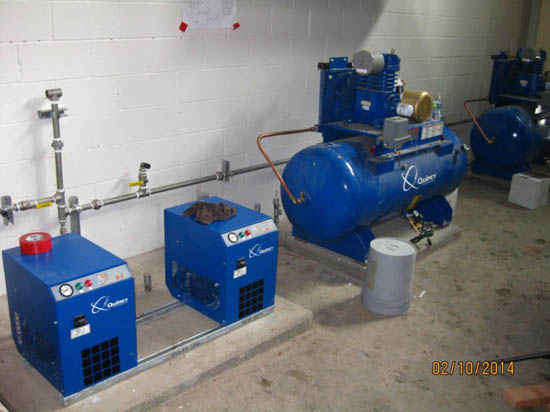
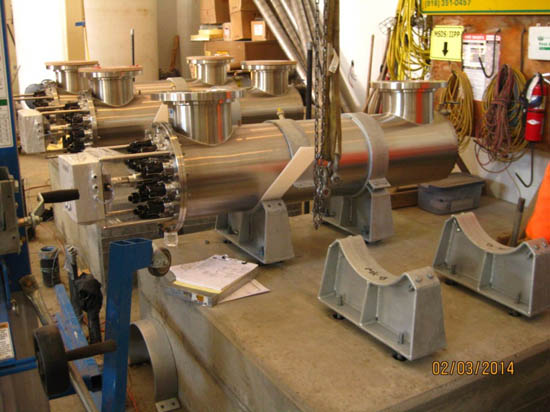
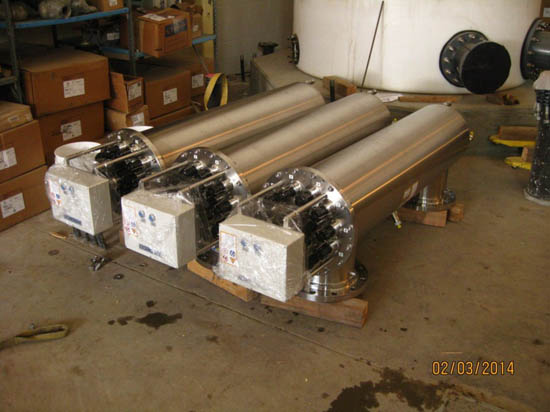
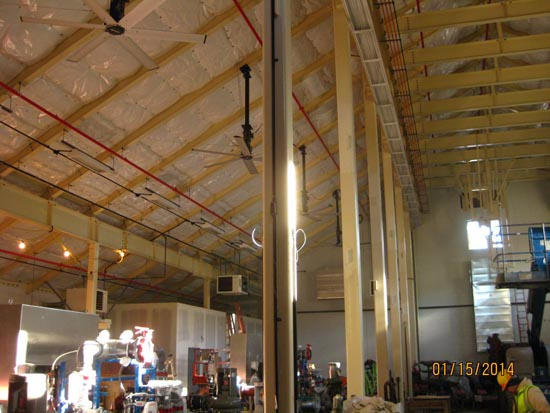
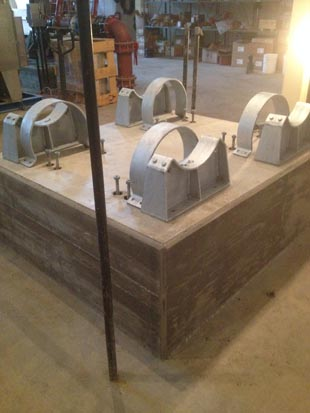
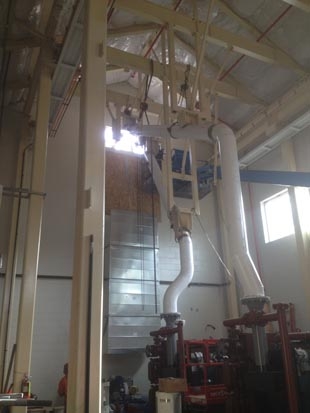
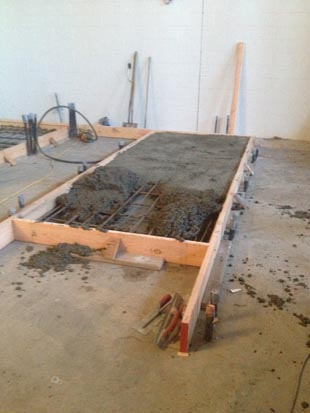
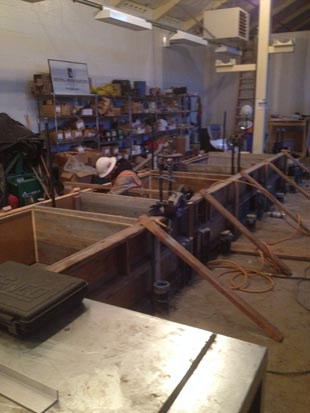
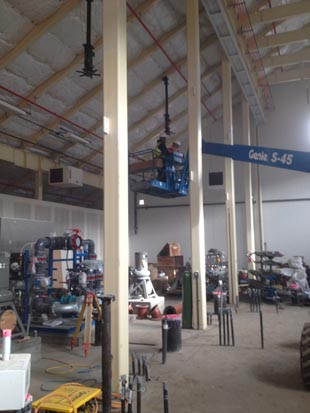
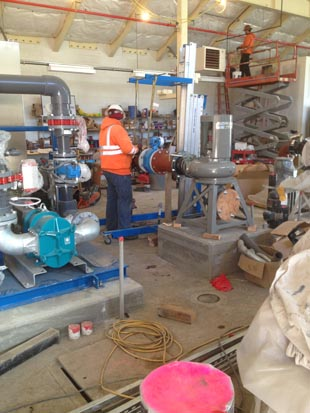
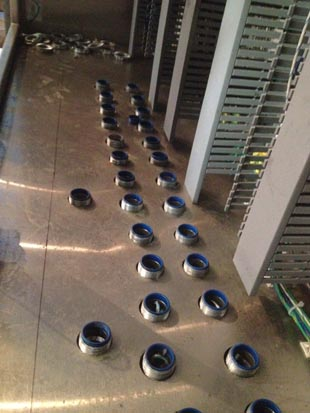
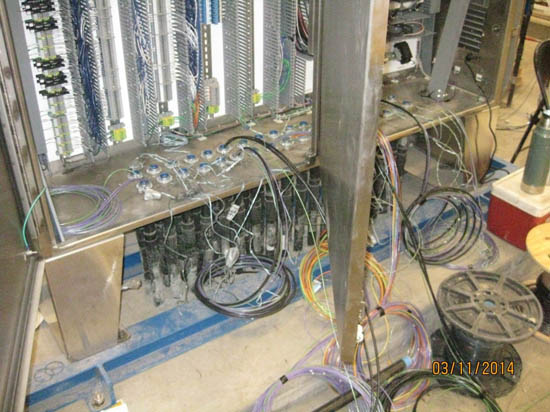
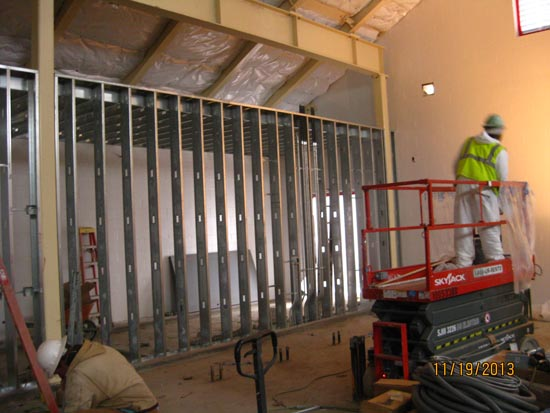
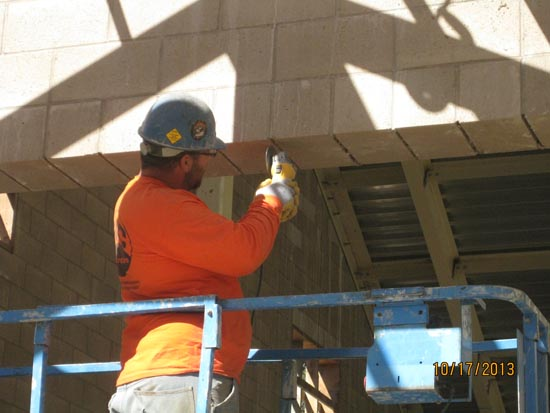
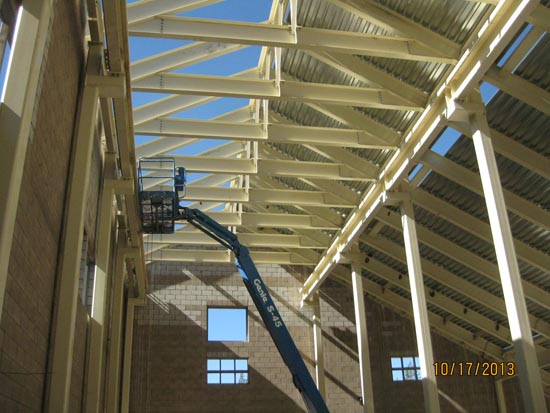
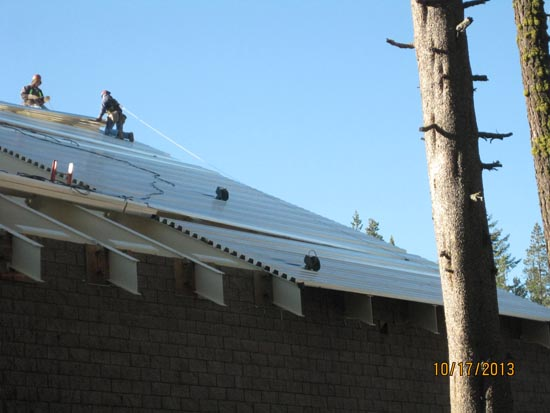
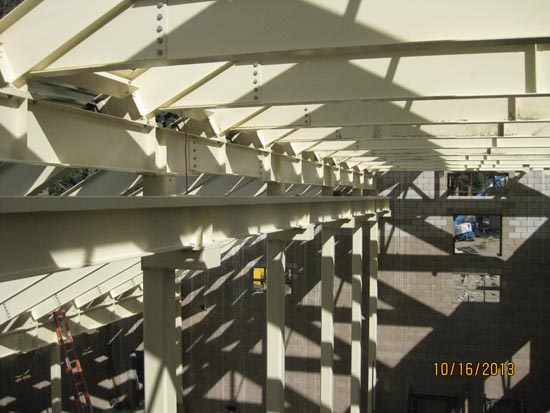
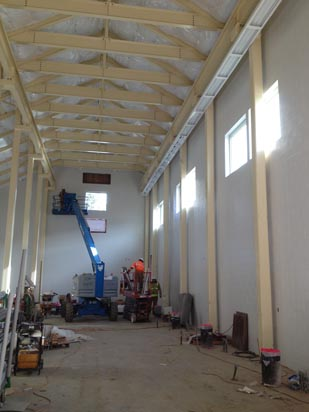
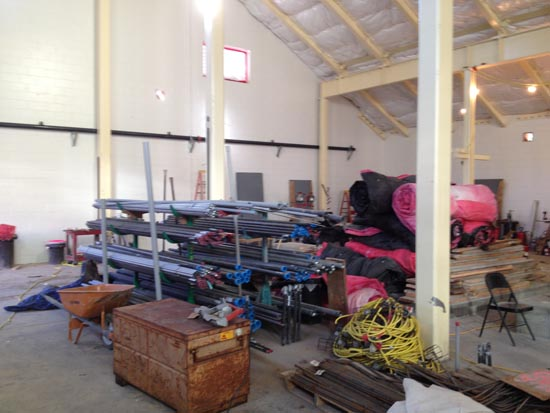
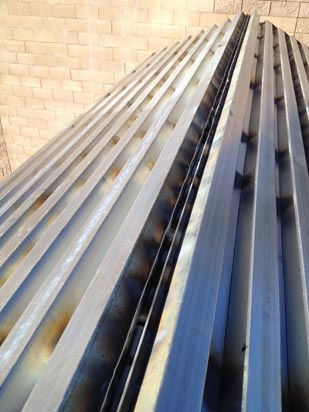
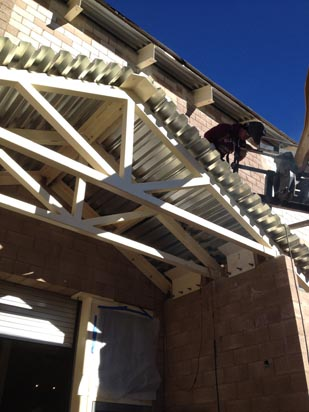
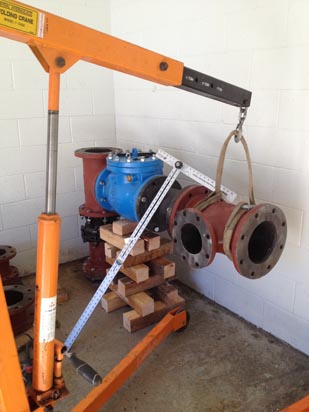
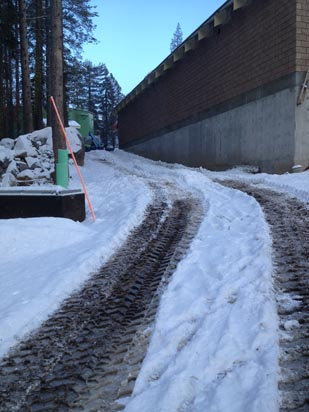
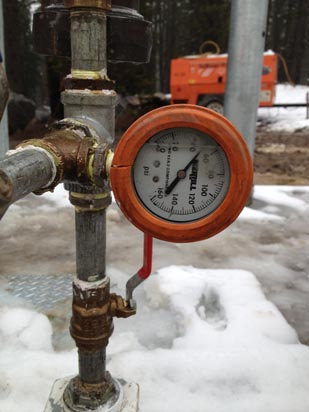
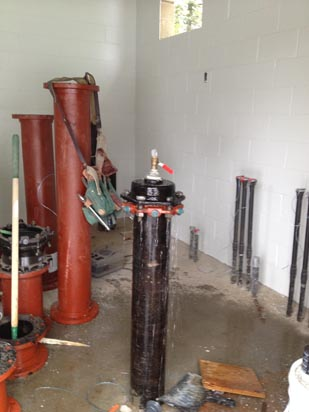
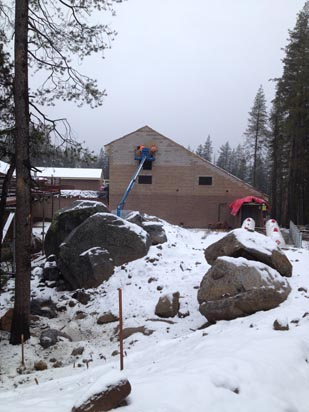
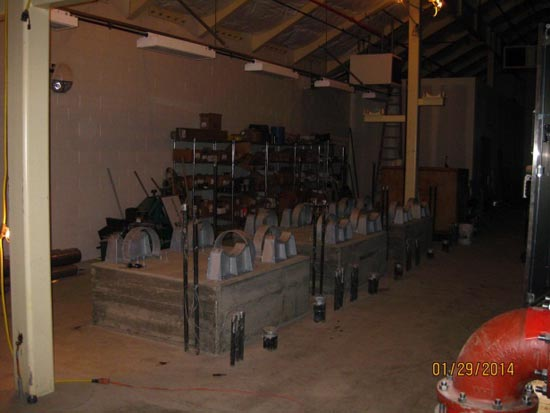
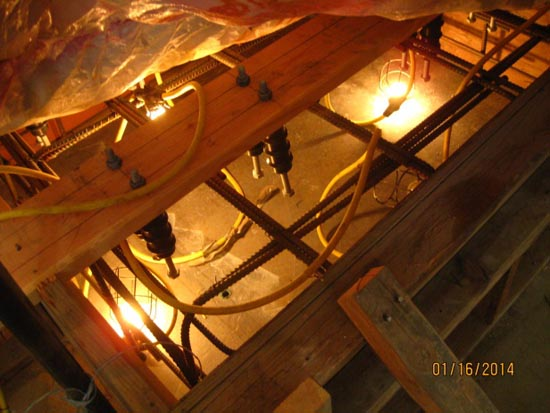
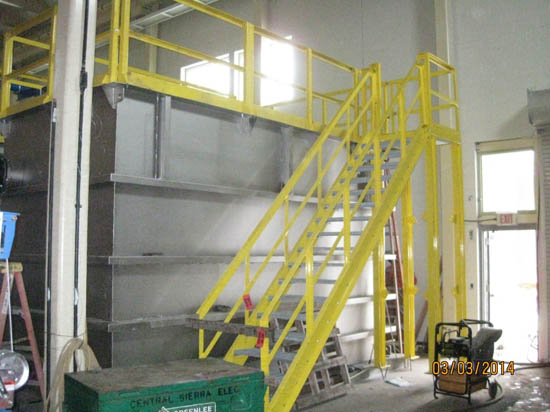
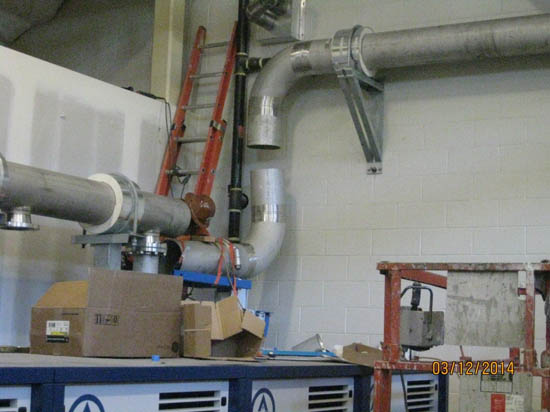
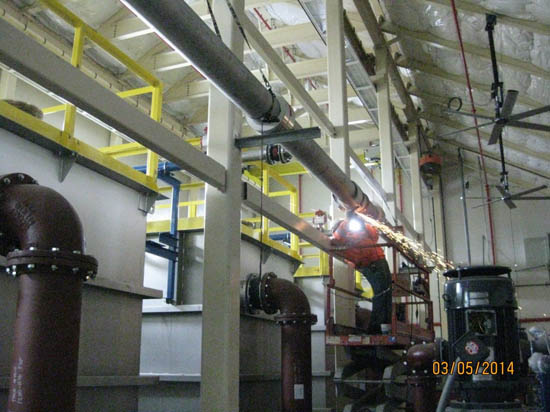
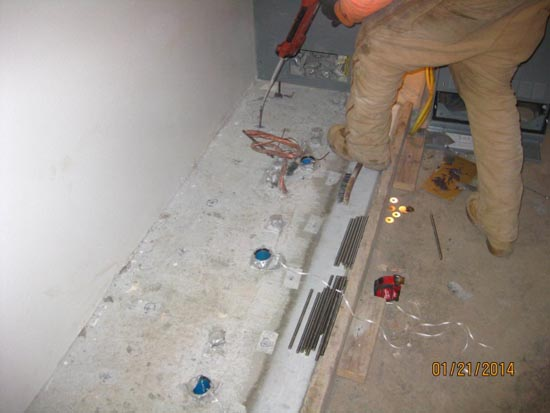
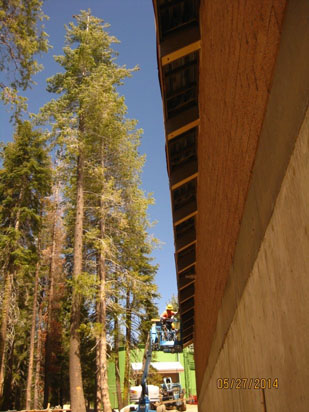
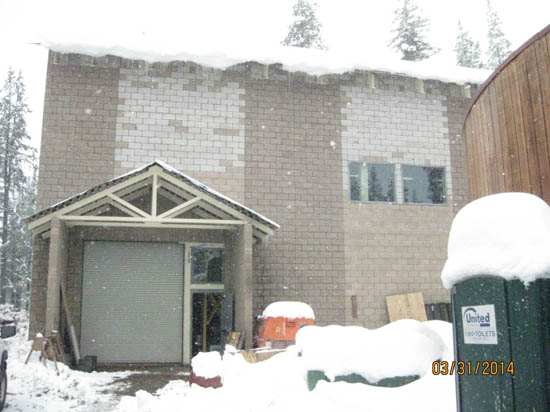
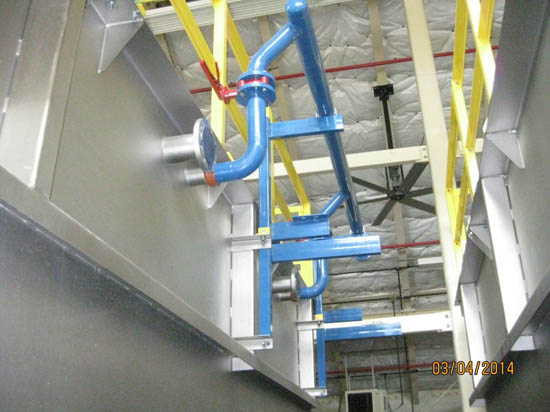
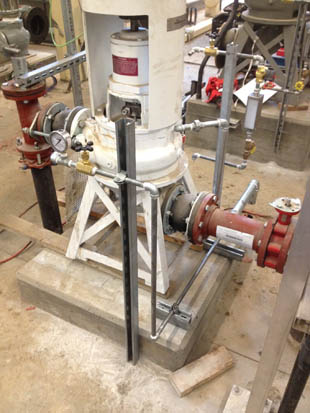
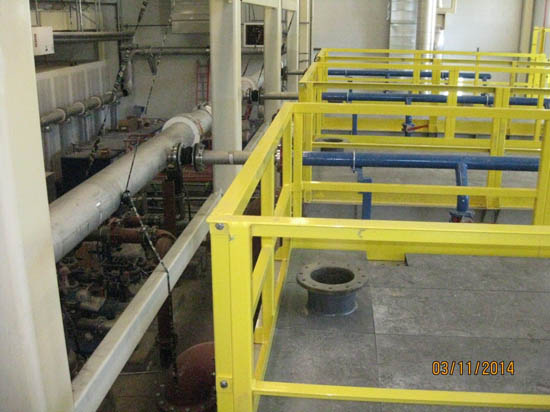
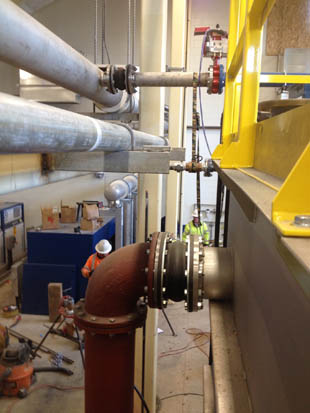
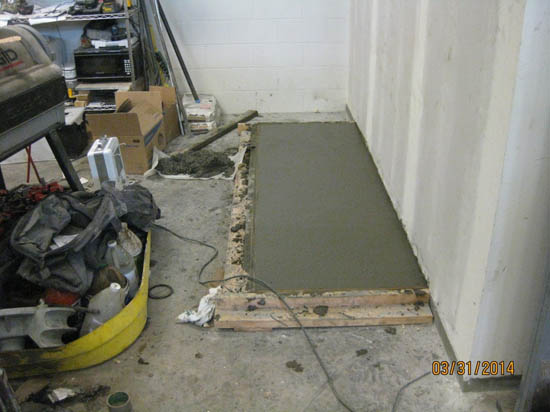
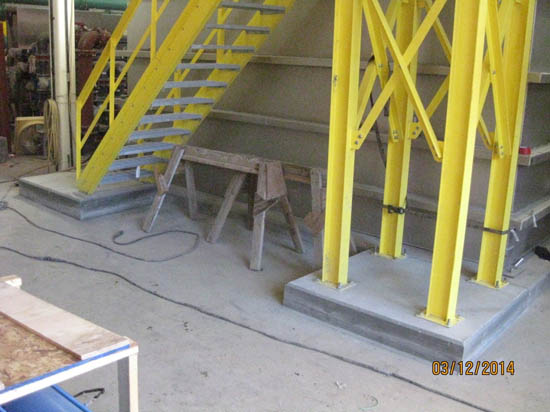
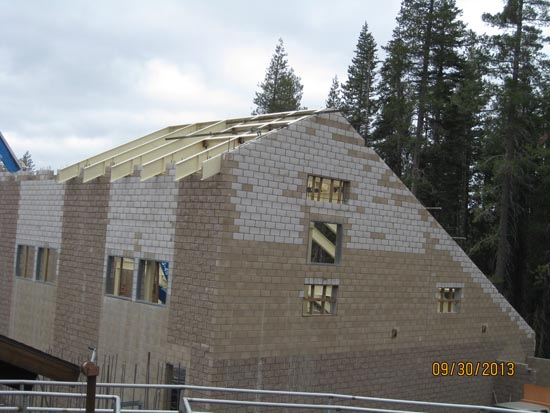
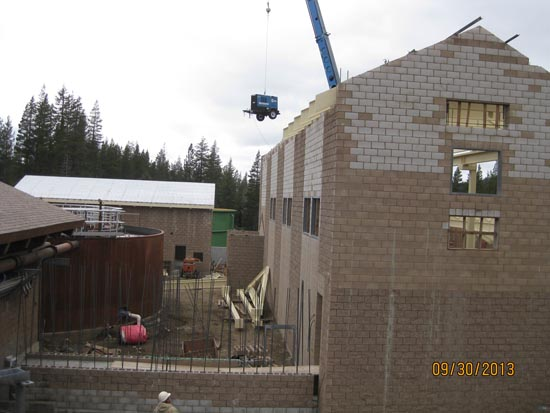
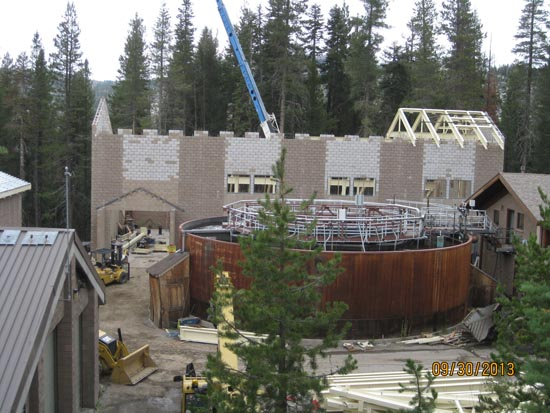
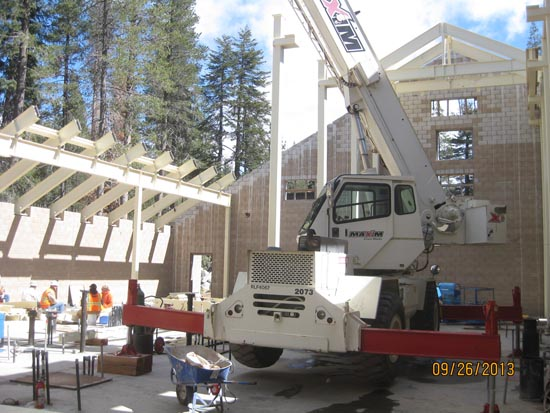
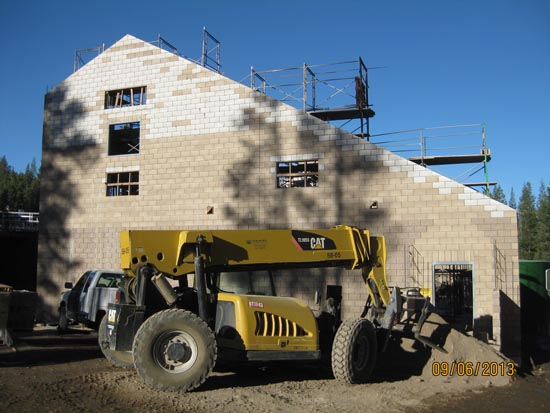
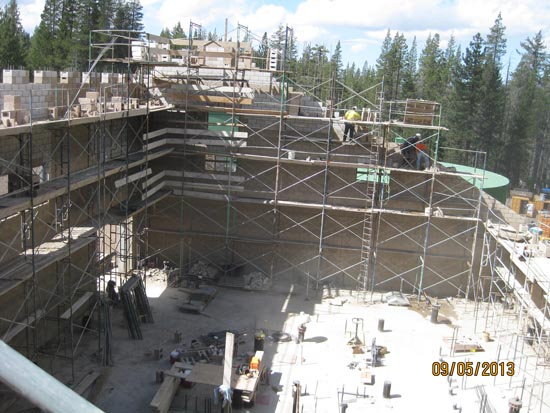
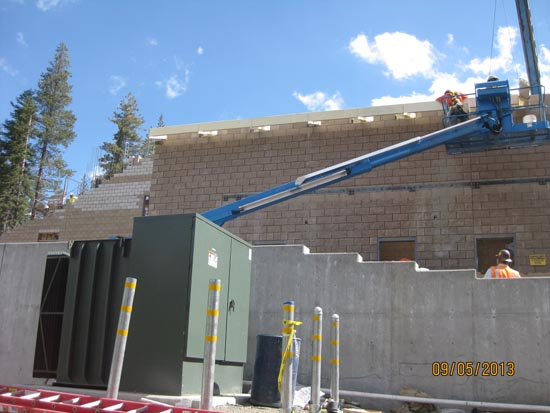
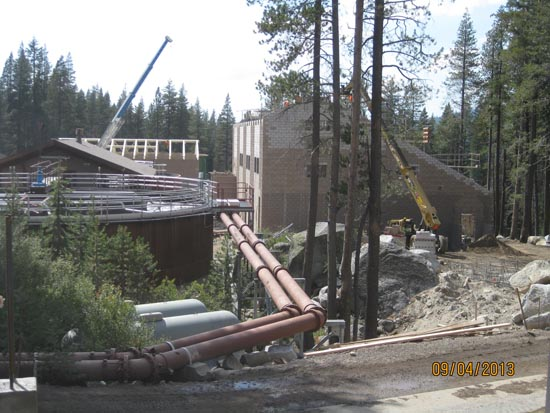
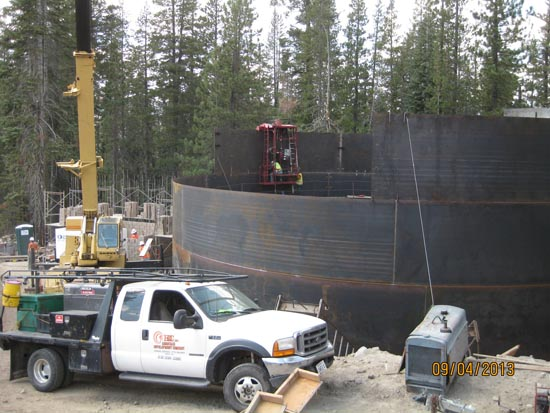
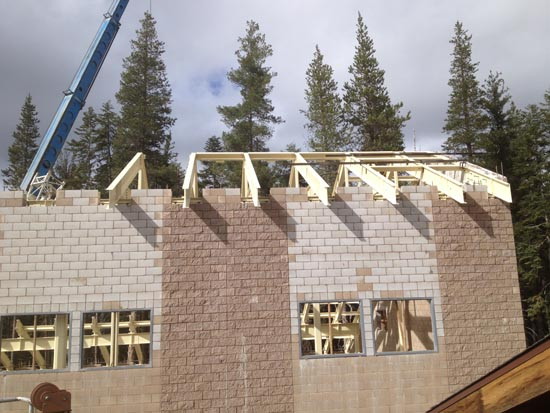
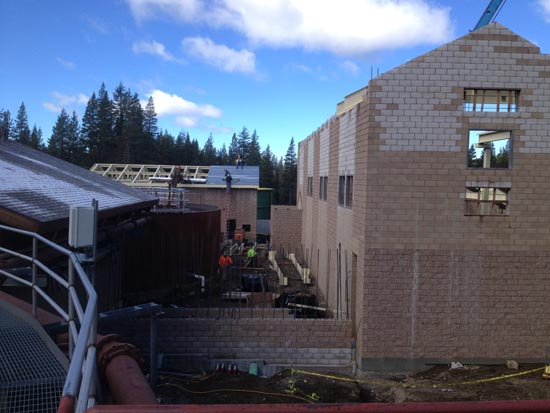
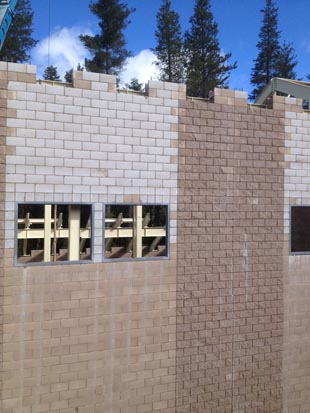
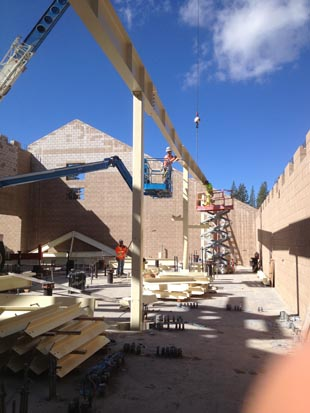
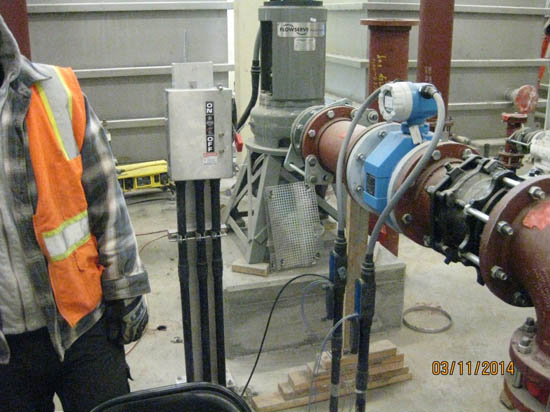
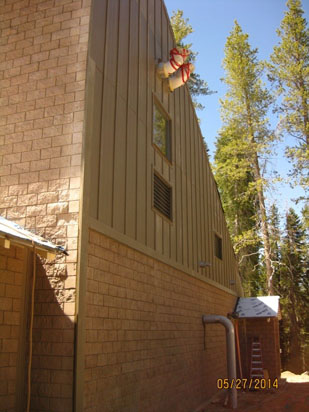
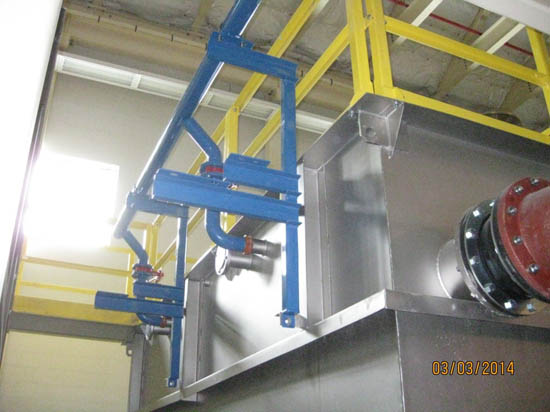
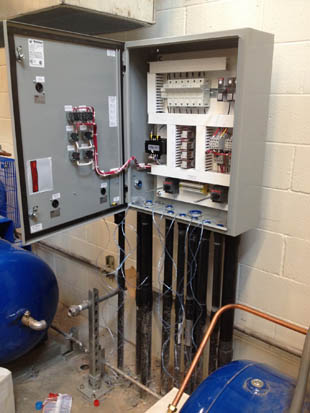
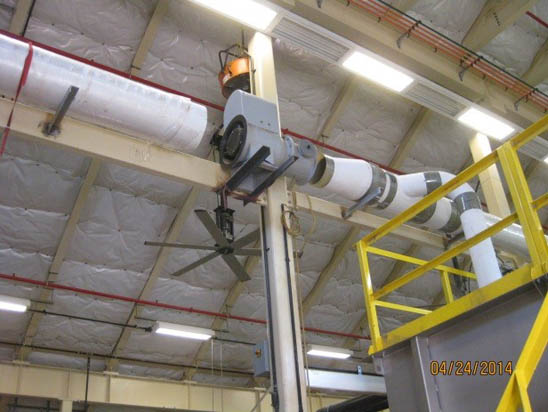
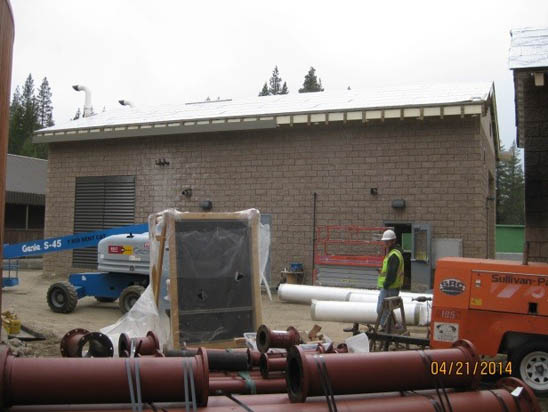
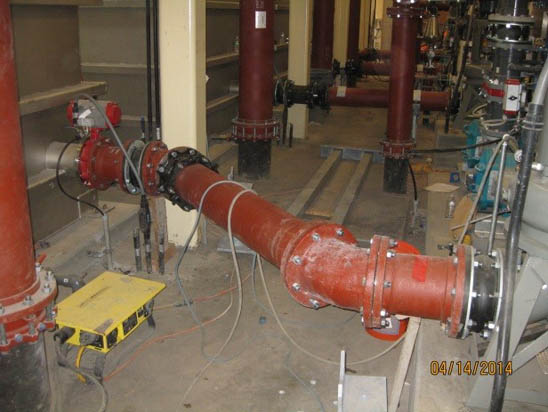
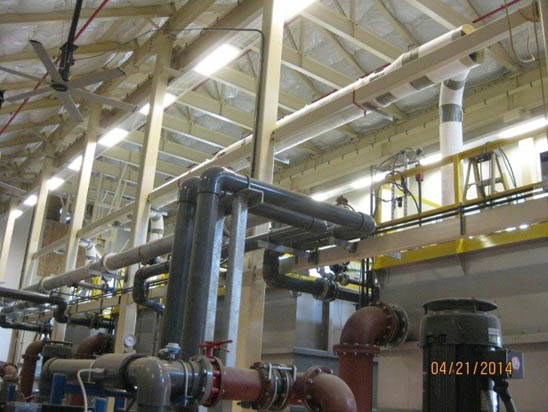
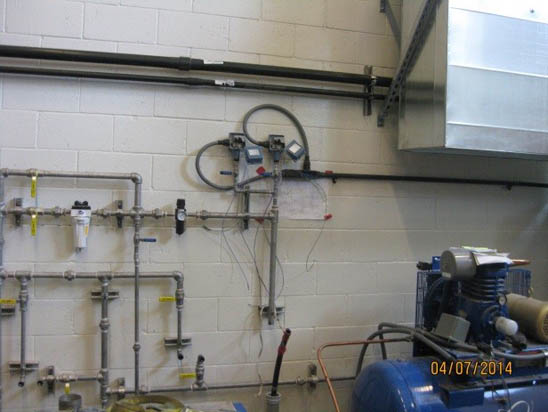
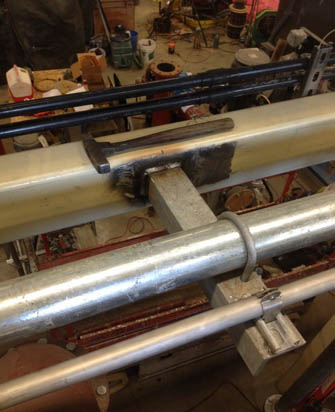
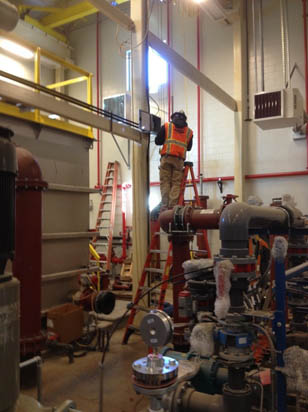
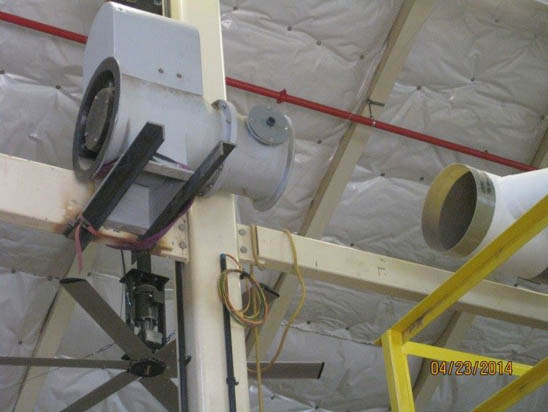
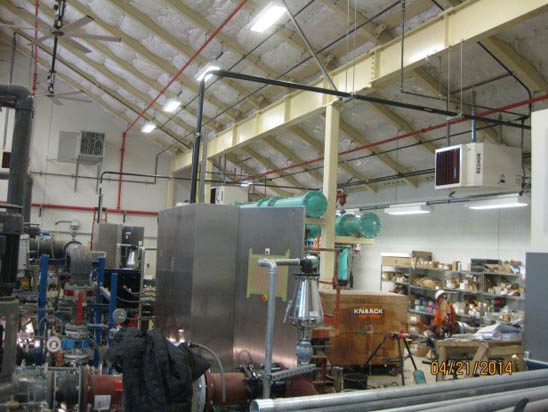
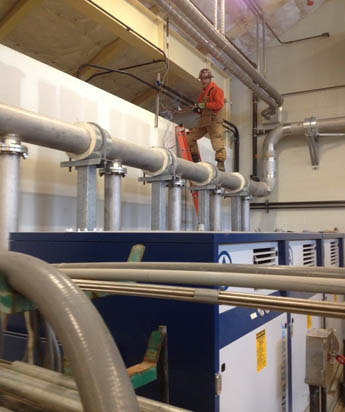
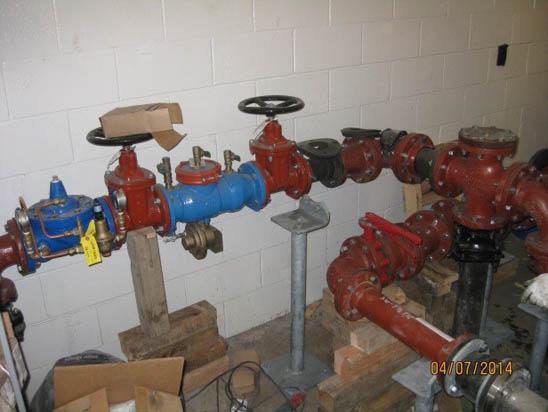
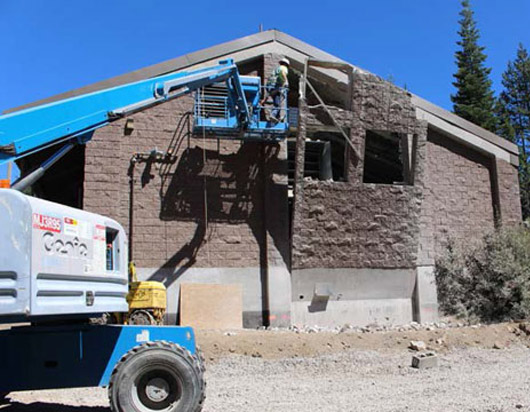
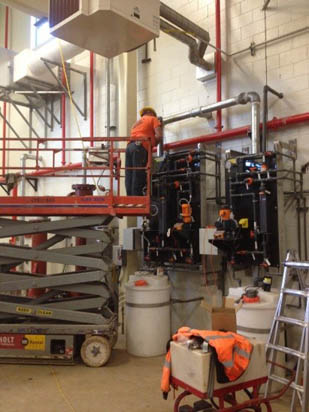
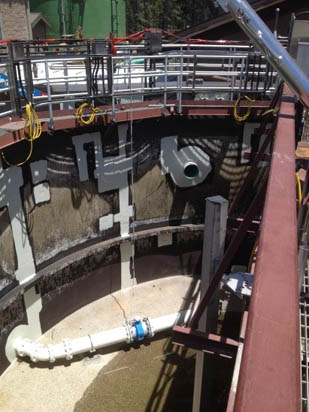
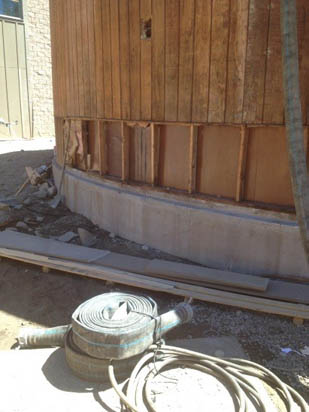
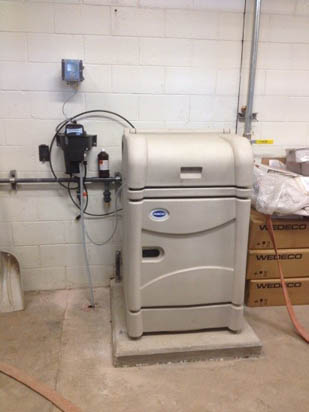
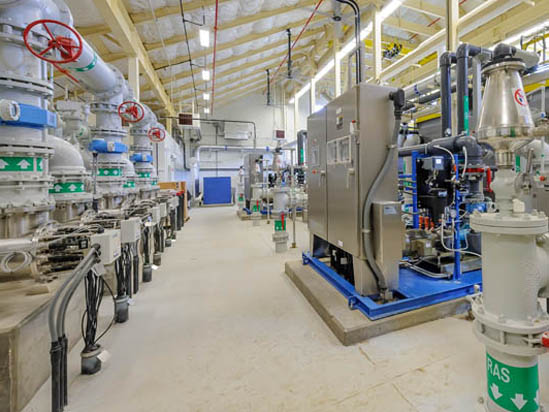
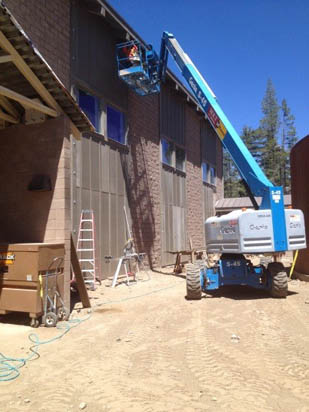
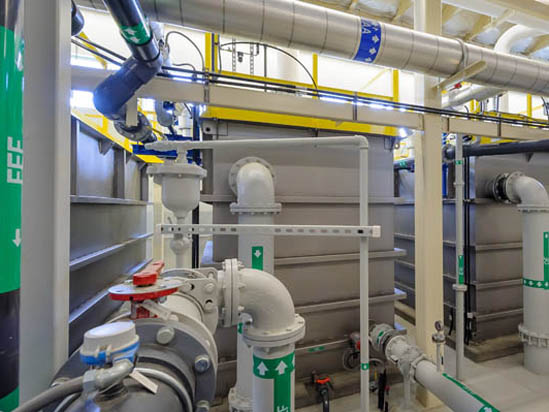
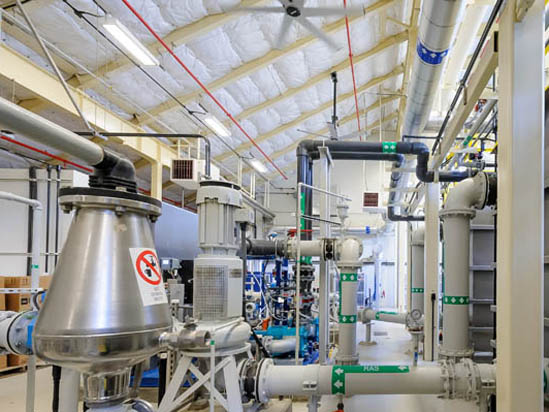
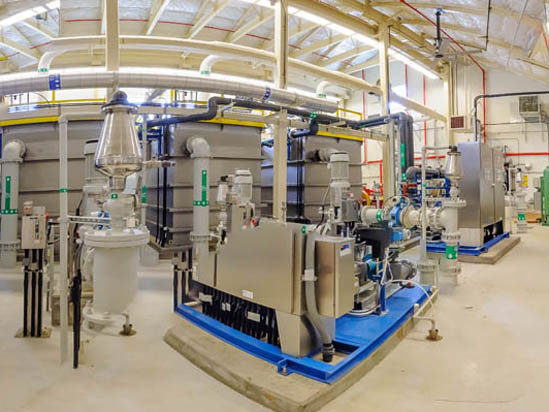
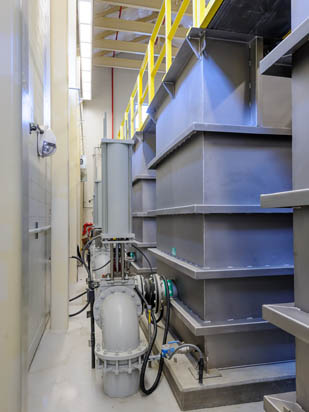
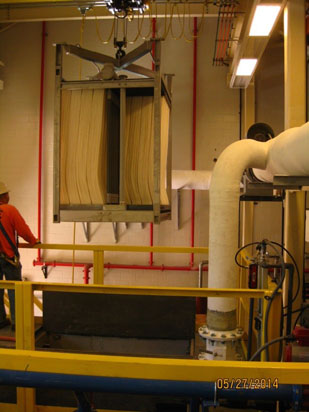
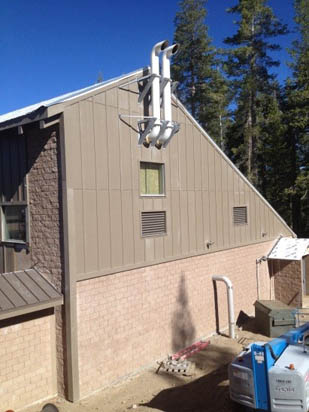
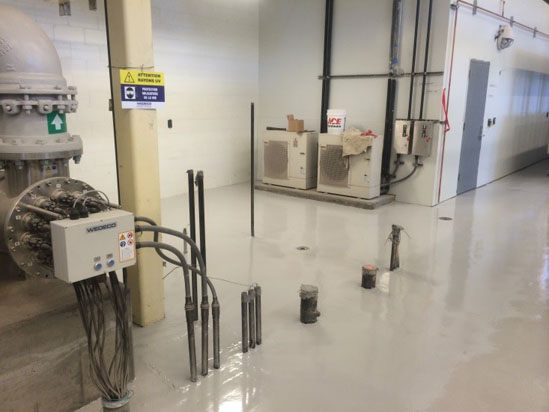
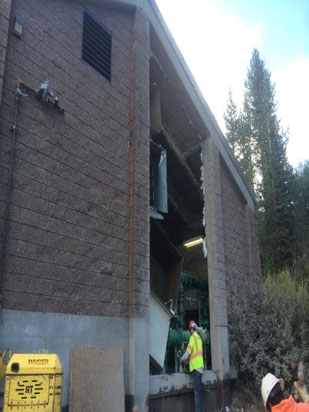
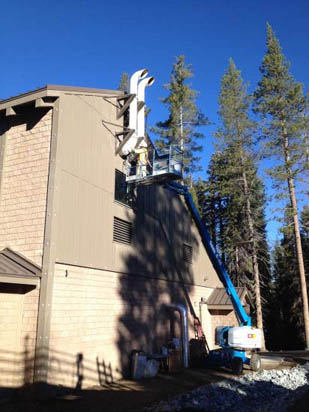
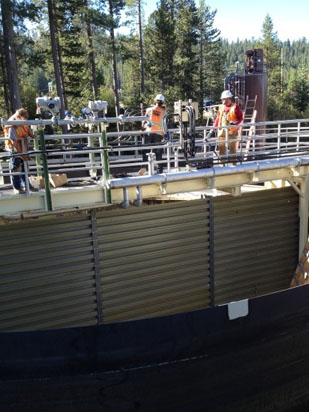
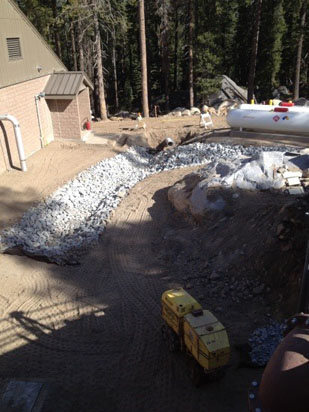
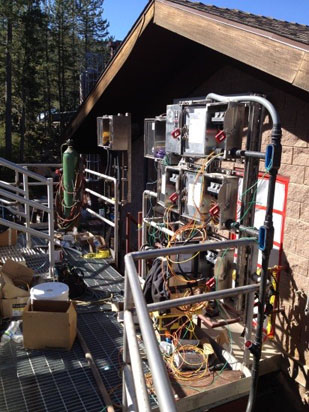
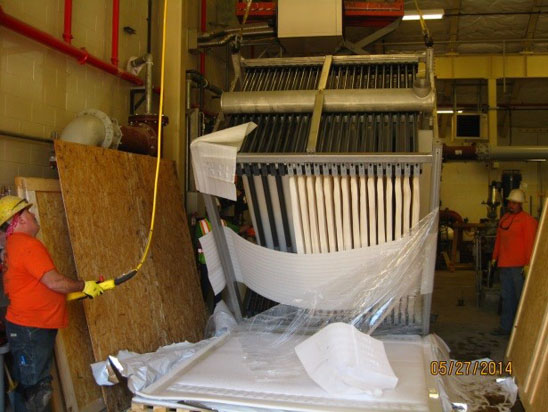
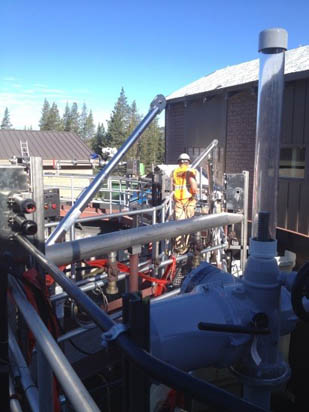
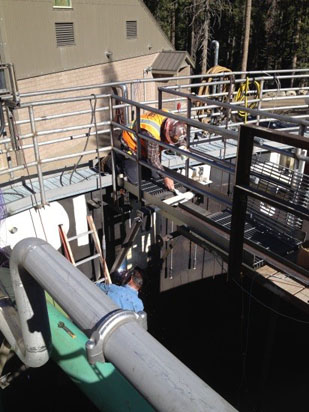
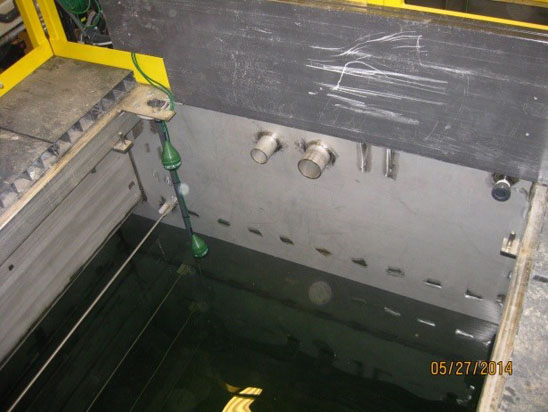
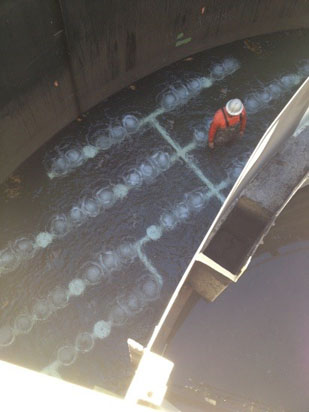
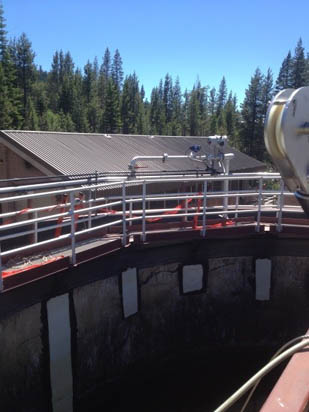
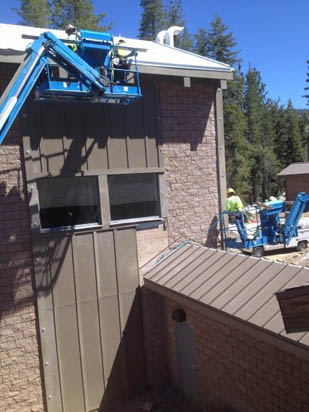
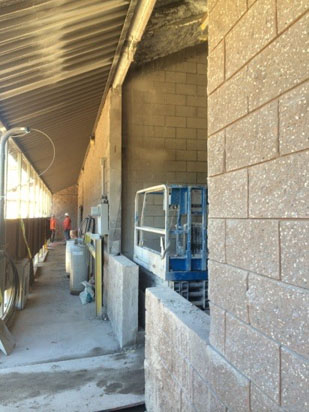
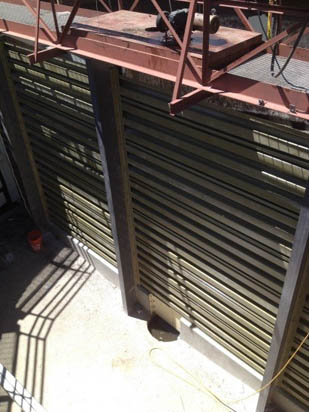
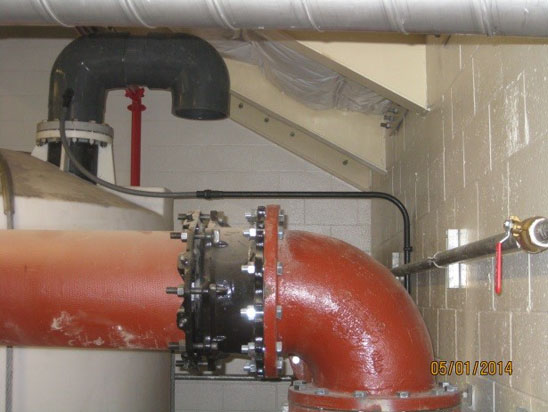
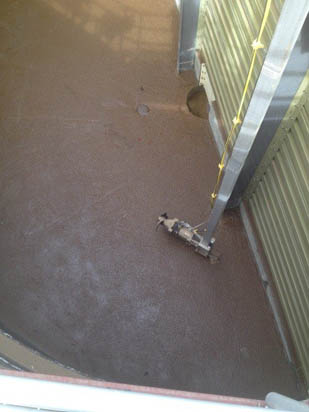
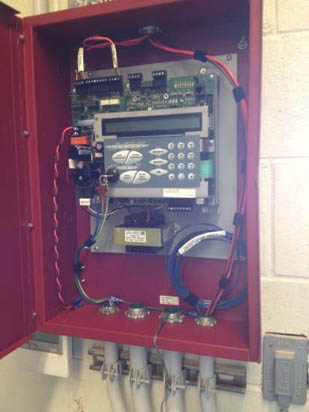
*Workers tying steel at the MBR building. Note the footing pedestals. The pedestals that are formed into the outer walls are like pilasters because of their construction, but pilasters typically would travel to the top of the wall and support the roof or wall. In the DSPUD building, there will be large structural steel tube columns (10î and 8î square) that will mount on the shown anchor bolts located at the top of the pedestals at floor level, and support the overhead bridge crane and the roof. See additional photos of concrete forming around bolts.